Take the Blindfold Off Your Warehouse Operation
The OneTrack Guide to Forklift Safety
Learn how to build a video-based (and data-driven!) forklift safety program that will help you reduce MHE incidents, coach operators, eliminate false workers comp claims, and save money.
Something BIG Is Happening 4/17 That'll Change Warehousing For Years To Come
‍
Success Story
See how this 3PL captured value from their forklift safety program
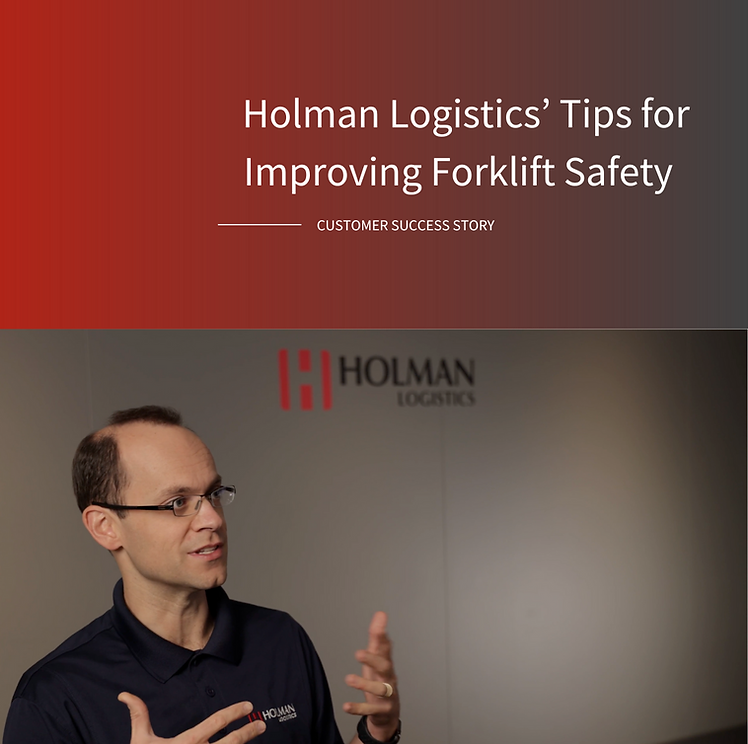
‍
Learn how Holman Logistics, a leading 3PL in North America, is using a video based forklift safety program to coach their operators, reduce costs, and keep their warehouses safe.
‍
‍
‍
‍
Ensure every operator clocks out safe after every shift
OneTrack's AI Forklift cameras and safety tools give logistics leaders the visibility they need to help reduce forklift accidents, improve operator behavior, and lower costs. Explore how our Warehouse Intelligence platform can help you improve safety and drive ROI.
AI Forklift Cameras
Protect your warehouses and keep people safe with AI forklift cameras that monitor MHE for risks 24/7 and send real-time video alerts to help keep operations running smoothly.
Dynamic Labor Management
Engineered labor standards are broken. Improve productivity in your warehouses by using AI to proactively alert you of risks, track your labor processes, and connect WMS timestamps with video context to make critical process improvements.
Proactive Operator Coaching
Coaching shouldn't ONLY happen after a major incident. Get alerts of the leading indicators of MHE safety incidents to coach operator behavior proactively and change the culture in your warehouses.
‍
“OneTrack helps us keep the entire team safe, and that's what we need at the end of the day. It's one of the best products out there that I've seen and that I've worked with.”
Lina Recker
Corporate Compliance Manager
Spartan Logistics
‍
Not sure where to start?
Start by picking the right technology to meet your goals. Learn why forklift cameras are worth the investment, and see how to pick the right forklift safety system for your warehouses.
‍
Chapter 1: Select the Best Forklift Cameras for Your Warehouses
‍
Why invest in forklift safety cameras?
If you rely on forklifts and other MHE in your warehouses, you need to consider investing in a forklift safety system. AI forklift cameras bring deep visibility into operations so supervisors can coach operators, EHS leaders can build robust forklift safety programs, and logistics leaders can drive real ROI from warehouse safety.Â
‍
3 reasons to invest in forklift cameras
- 70%+ of forklift accidents are preventable (OSHA)
- 90,000+ forklift related injuries each year
- 10%+ of forklifts are involved in an accident each year
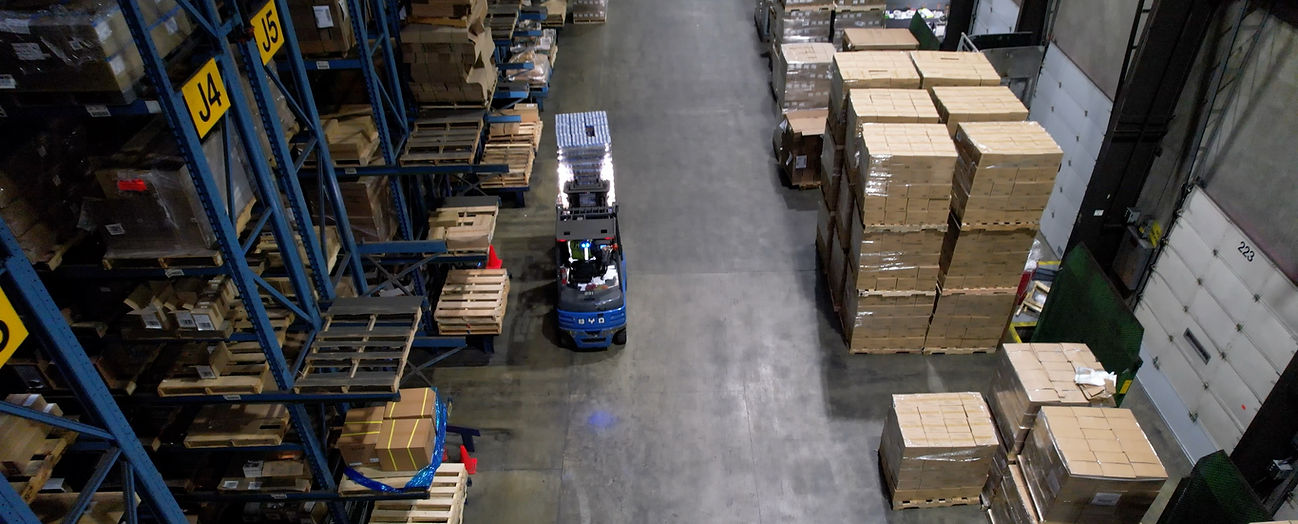
Something BIG Is Happening 4/17 That'll Change Warehousing For Years To ComeÂ
‍
The benefits of forklift camera systems for logistics leaders
01. Never miss an incident in your warehouses
AI forklift cameras can be your eyes on the floor at all times. You get real-time, video-based notifications of every safety incident in your warehouse. Proactively coach your operators to improve the behaviors in your warehouse – from hard forklift impacts, phone use, product hits, and everything in between.
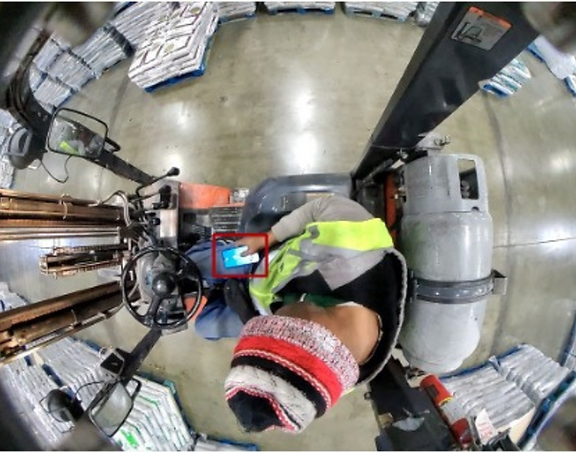
‍
02. Improve warehouse accountability
Once you start coaching your operators, it will completely shift the culture in your warehouses. Operators will start self-reporting incidents to supervisors, they will start stepping up and holding each other accountable for safe and productive work. Supervisors will get better at having tough conversations and become true safety champions in your buildings.
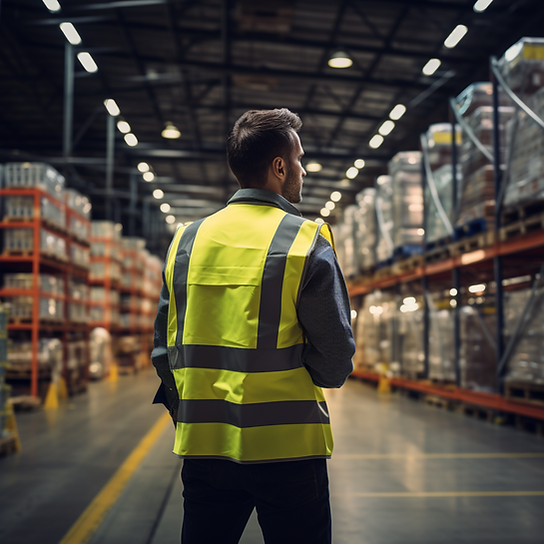
‍
‍
03. Decrease unplanned MHE maintenance
You expect a certain level of MHE maintenance every year. But when forklift impacts start creeping up, racking gets damaged, and unsafe dockplate maneuvers start damaging tires — these maintenance costs can skyrocket. With a forklift camera system, you can cut down on this forklift wear and tear to keep your fleet (and budget) in top condition.
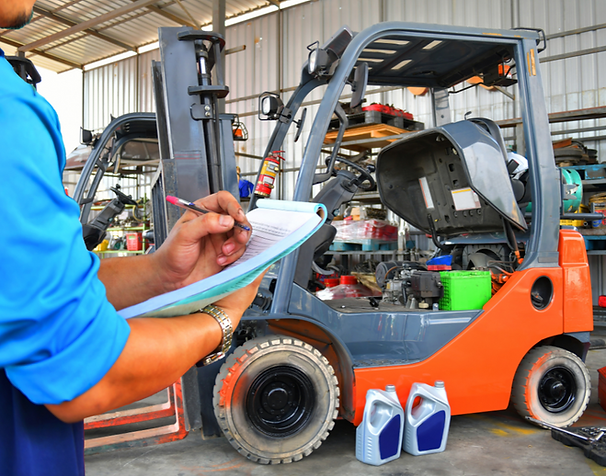
‍
04. Avoid false workers comp claims
Unfortunately, in warehouses workers comp claims are a fact of life. And it’s your job to investigate, collect evidence, and provide that to the insurance company. Just imagine if you had concrete video evidence to turn for every investigation. No more cycling though hours of CCTV footage or getting conflicting reports. Streamline your safety investigations and eliminate unnecessary payouts with AI forklift cameras.
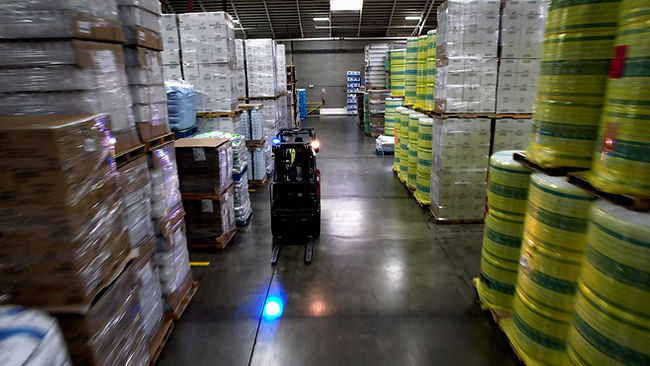
‍
05. Minimize labor costs and turnover
Forklift camera systems can actually reduce labor costs in a few ways. For starters, after the initial rollout and operator buy-in there’s a huge culture change that comes. Operators know that safety is a priority and turnover goes down. Plus, with digital operator scorecards and video-based coaching tools, your supervisor team can upgrade their coaching conversations, and even streamline recruiting and onboarding top talent.
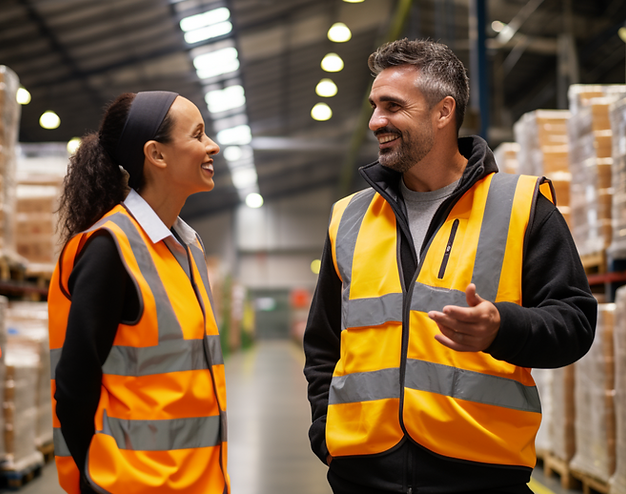
‍
‍
In this chapter:
01. Understand the technology: What are forklift camera systems?
02. Evaluate your options: What are the different forklift safety options?
03. Select the right vendor: What to look for in a forklift safety system?
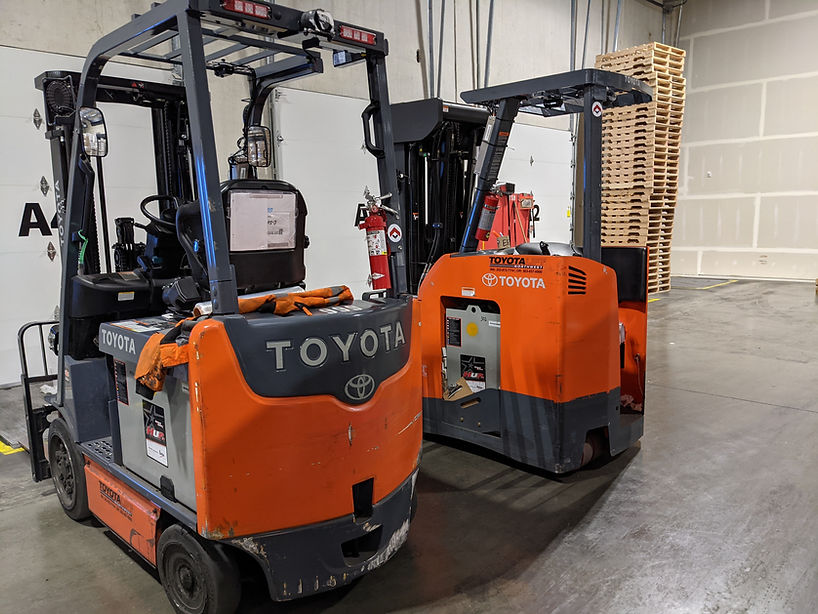
Part 1 — Understand the Technology
What are forklift camera systems?
Forklift camera systems are incredibly powerful tools to help improve your forklift safety programs. Especially when combined with AI. From coaching MHE operators to investigating workers comp claims, they can be used in a number of ways to greatly improve safety in your warehouses and can even help you reduce costs.Â
​
How forklift camera systems work
These systems work by mounting cameras on forklifts and other MHE equipment to capture footage of the operator and the surrounding area of the lift. The best forklift camera systems go beyond traditional GForce and telematics and use artificial intelligence (AI).Â
These safety systems use AI to monitor MHE equipment 24/7 (without needing to dedicate manpower). With AI, the system can detect a number of different safety events like impacts, harsh brakes, phone use, product damage and more. These systems automatically alert operations leadership to help provide better visibility and upgrade operator coaching and safety investigations.
‍
Expert Panel
How 3 Logistics Leaders Use AI Forklift Cameras to Improve Warehouse Safety
Hear stories from real logistics leaders about how they use technology to keep their warehouses safe and productive.
‍
Part 2 — Evaluating Your Options
What are the different forklift safety solutions available?
Not all forklift safety solutions are created equal. There are a number of different tools available, but what’s the best option for your warehouse? Let’s take a look.
‍
Forklift telematics systems
Forklift telemetry systems use a GForce threshold to notify you when an impact occurs and lock out a lift. Unfortunately, GForce is a static number. It can’t differentiate between a dockplate, a crack in the floor, or an impact, which can lead to false positive triggers.
This forces logistics teams to turn down the GForce threshold on their forklift telematics to a point where many safety events, impacts, and product hits slip through unnoticed.
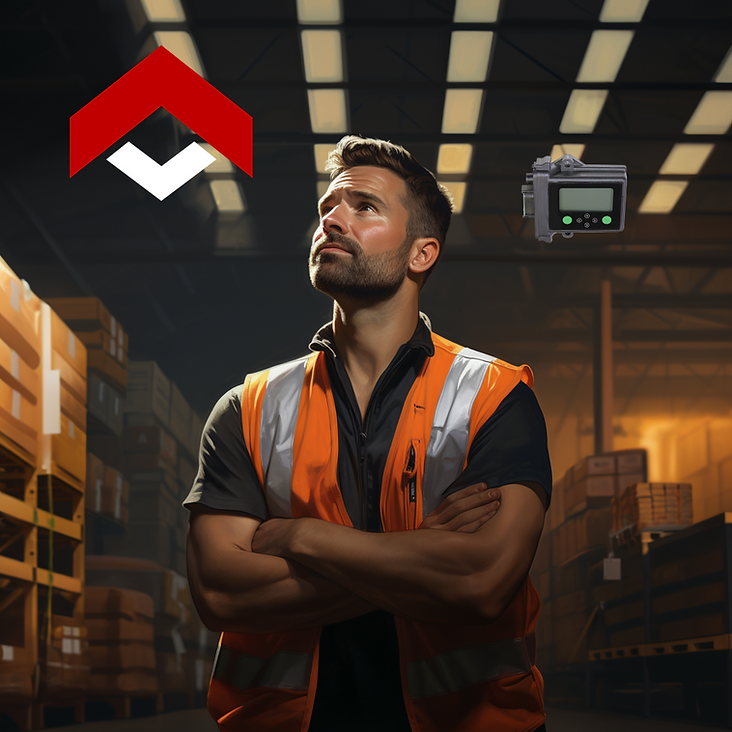
Proximity alarms and pedestrian monitoring systems
These work a lot like your cars back-up camera. These proximity alarms produce an audible beep whenever the lift gets too close to something, and some systems can even slow down a lift whenever pedestrians are near.Â
These are great supplemental tools for a forklift safety program, but it’s like putting a bandaid on a bullet hole. Without addressing the root cause (operator behavior and accountability), nothing will really change.
AI forklift camera systems
AI forklift camera systems (like OneTrack) learns your unique warehouse processes and alerts you when things like forklift impacts or product hits occur. Beyond that, it allows you to be proactive instead of reactive after an incident.Â
‍
OneTrack is able to detect leading indicators of safety events, phone use, idle time, and can even monitor lift utilization and digitize your pre-flight inspections. We then give you robust reporting to help coach operators, improve process using data, and create the safest and fastest warehouses on the planet.
‍
Different camera configurations for your forklift safety program
Overhead
The overhead camera is the bread and butter of a good forklift camera system. This should provide you with a clear image of the operator as well as a 360° field of view around the MHE. The overhead camera is designed to provide actionable coaching opportunities by showing what an operator was doing when an impact occurred, or what process barriers may have led to an incident.
- 360° overhead view
- Video coaching
- Environment monitoring
- Leading indicators & near misses
‍
EPJs
Similar to the overhead camera, it is possible to mount OneTrack AI cameras on electric pallet jacks (EPJs) and nearly any other type of MHE. This provides you with the same clear image of the operator that you get with a standard fork or clamp truck mounting, as well as a 360° field of view around the MHE.
- 360° overhead view
- Video coaching
- Case pick monitoring
- Leading indicators & near misses
‍
Forward facing
Forward facing (or front facing) cameras are becoming more and more popular. From a quality standpoint these cameras are very powerful when it comes to costly processes like load validation. For your safety program, this can also provide a good POV when incidents happen, and you can even request that footage to help with a safety investigation that the MHE wasn’t involved with, but was potentially in the area.
- Load validation
- Quality checks
- Workstation monitoring
- First person POV for impactsStationary
Stationary cameras are typically mounted in the ceiling of a warehouse to monitor dock doors and staging areas. Great from a productivity monitoring standpoint but can also give you a birds eye view of critical areas in your warehouse and show safety incidents from a more holistic view. This shouldn’t be confused with traditional security cameras, as the AI is specifically trained to identify events related to safety, productivity, and quality — not necessarily security.
- Dock-door and load monitoring
- Free-space monitoring
- Proximity alerts
- Heatmap traffic monitoring
- Case pick tracking (with WMS)
Yard Trucks
The overhead camera is the bread and butter of a good forklift camera system. This should provide you with a clear image of the operator as well as a 360° field of view around the MHE. The overhead camera is designed to provide actionable coaching opportunities by showing what an operator was doing when an impact occurred, or what process barriers may have led to an incident.
- 360° overhead view
- Video coaching
- Environment monitoring
- Leading indicators & near misses
‍
Different forklift camera system features
Once you've landed on what forklift camera configurations best fit your needs, you'll also want to think about some of the most important features forklift camera systems offer as you evaluate vendors. From artificial intelligence to customizable analytics, here are the top forklift safety features to look for.Â
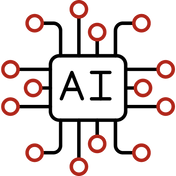
Artificial intelligence (AI): The best forklift safety systems are built with artificial intelligence at their core. AI makes it possible to go beyond just GForce to detect critical safety events and unlocks the ability to coach operators on leading indicators and near misses.
‍
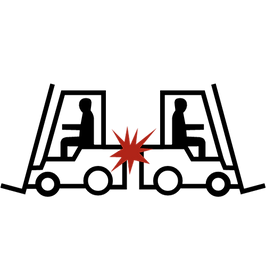
Impact detection: The best forklift camera systems eliminate the feeling of coming into work, finding out there was an incident, and then when asked about it, saying “I don’t know”. And it shouldn’t just detect hard impacts. Soft impacts and rack bumps lead to more wear and tear, and therefore more maintenance dollars spent.
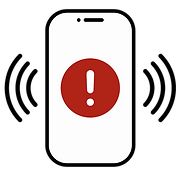
Real-time alerts: It doesn’t do much good to coach weeks after an event takes place. The best forklift camera systems send out alerts within minutes of a safety incident occurs, so your supervisor team can have prompt coaching conversations while the details are still fresh.Â
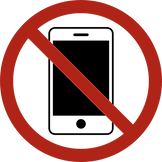
Leading indicators and near misses: The real differentiator between an AI system like OneTrack and a traditional forklift safety system. OneTrack is able to pick up on leading indicators and near misses (like not looking in the direction of travel or phone use during operation) so you can proactively coach operator behavior, before an accident ever happens.
‍
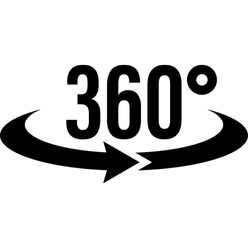
Field of view: This is what the forklift camera will actually see — and what you’ll see when an alert comes through! You want a good field of view, without compromising on resolution or angle. OneTrack uses a proprietary lens to maximize for both - giving you a crisp 360° view of your MHE.
‍
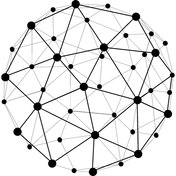
Internet connectivity: The beauty of an AI forklift safety system is that it doesn’t require someone to constantly watch footage and flag events. It does it automatically. But to get those alerts you need reliable connection. Cellular and wifi connectivity are must haves for your forklift camera system. With OneTrack we use a proprietary mesh network to ensure maximum connectivity.
‍
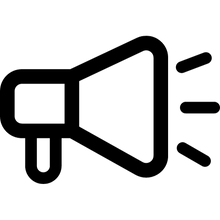
Audio alerts: It’s best to stay away from recording audio (for privacy concerns), but it is a good idea to have some sort of audio alarm built into your forklift camera. Similar to a seatbelt alarm in your car, this is an audible reminder for operators to complete their pre-flight OSHA inspections, when they travel into a restricted zone, or even for pedestrian detection.Â
‍
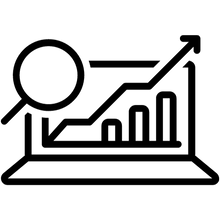
Customizable analytics: Video alerts are an amazing capability for site level improvements, but to make real change on a network level you need to unlock your data to spot safety trends. A system like OneTrack becomes your single source of truth for all warehouse data, with powerful out of the box Leader Standard Work dashboards, plus the ability to build custom reports to meet your needs.
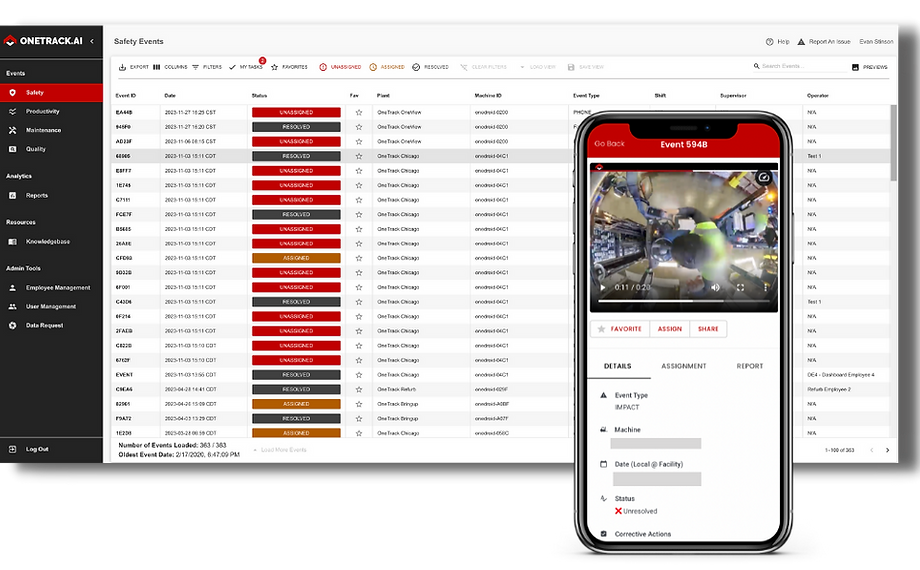
‍
See how OneTrack AI Forklift Cameras Improve Warehouse Safety
Ensure all warehouse employees clock out safe after every shift with AI forklift cameras that analyze MHE in real-time and automatically alert your team of safety events with video evidence. ​
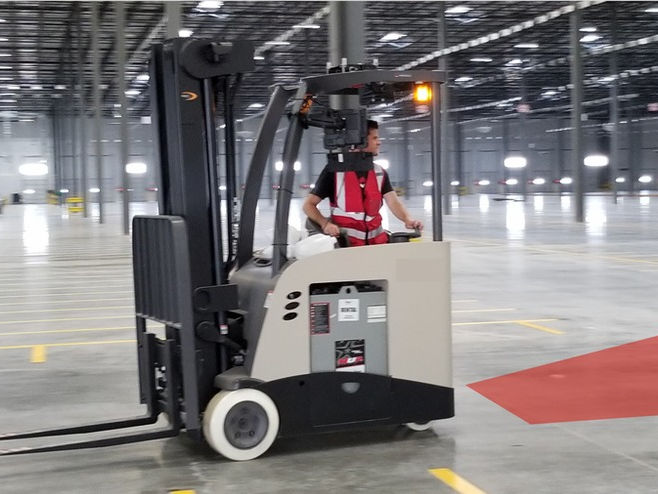
Part 3 — Select the Right Vendor
What to look for in a forklift safety system?
With so many different solutions out there, it’s impossible to try everything. Instead, consider looking for a solution that combines the best features from each forklift safety category into one platform.Â
OneTrack’s Warehouse Intelligence platform offers AI forklift cameras, powerful forklift telematics, and AI labor management features all in one easy to use system.Â
Trusted by some of the safest and fastest warehouses on the planet, OneTrack monitors your operations 24/7, and within minutes of an event being detected, sends your team a video alert showing exactly what happened. This kind of deep visibility will help you take your forklift safety to the next level.
Currently evaluating forklift camera solutions? Book a custom demo today and see how an all-in-one forklift safety platform can improve your operations.Â
‍
Customer Story
How Hain Celestial Reduced Forklift Safety Events by 80% with OneTrack
Hear from Hain Celestial's Sr. Warehouse Manager about how he upgraded his forklift safety program with AI forklift cameras to keep people safe and productive.
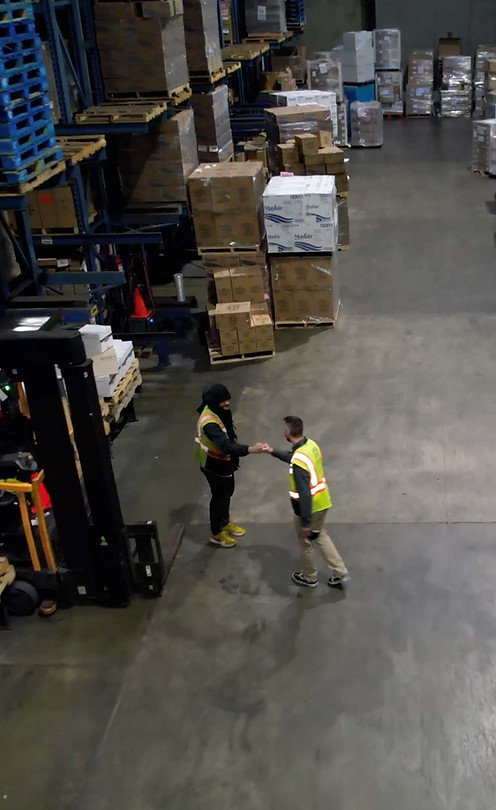
‍
Make forklift safety a priority with OneTrack
OneTrack's AI Forklift cameras and safety tools give logistics leaders the visibility they need to help reduce forklift accidents, improve operator behavior, and lower costs. Explore how our Warehouse Intelligence platform can help you improve safety and drive ROI.
AI Forklift Cameras
Protect your warehouses and keep people safe with AI forklift cameras that monitor MHE for risks 24/7 and send real-time video alerts to help keep operations running smoothly.Â
Dynamic Labor Management
Engineered labor standards are broken. Improve productivity in your warehouses by using AI to proactively alert you of risks, track your labor processes, and connect WMS timestamps with video context to make critical process improvements.Â
Proactive Operator Coaching
Coaching shouldn't ONLY happen after a major incident. Get alerts of the leading indicators of MHE safety incidents to coach operator behavior proactively and change the culture in your warehouses.Â
‍
‍
Chapter 2: Build an Effective Forklift Safety Program (Backed by Data)
‍
Why create a forklift safety program?
A forklift safety program is a coordinated, strategic effort that combines AI forklift camera systems with enhanced video coaching to improve operator behavior, reduce accidents, improve warehouse culture, and increase the life of your MHE. Read on for a step-by-step guide to build an effective forklift safety program from start to finish.
3 reasons to invest in a forklift safety program
- 70%+of forklift accidents are preventable (OSHA)
- 90,000+ forklift related injuries each year
- 48%+ fewer incidents at companies with strong safety cultures (HBR)
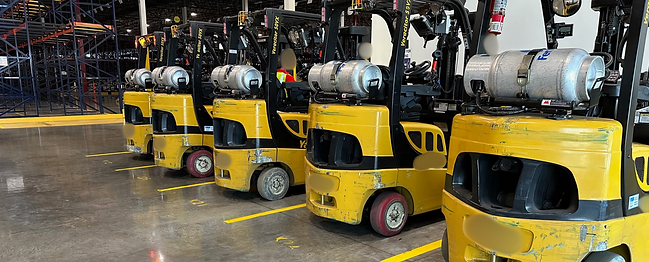
Something BIG Is Happening 4/17 That'll Change Warehousing For Years To ComeÂ
‍
In this chapter:
01. Before you begin: Invest in the right forklift safety system
02. Pre-launch planning: Set your goals and implementation plan
03. Implementation and rollout: Communicate policies and train your team
04. Day-to-day workflows: Improve operator behavior with video based coaching
05. Data-driven improvements: Use robust reporting to improve safety processes
‍
Part 1 — Before You Begin
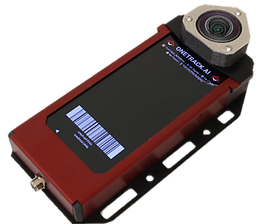
Invest in the right forklift safety system
A great forklift safety program relies on 3 things. Deep visibility, actionable data, and team buy-in. So before you begin, you need to invest in the right forklift safety system that can deliver that visibility and data you need.Â
The best forklift safety platforms —which should include AI forklift cameras, forklift telematics, and AI labor management — help reduce forklift safety incidents by more than 75% on average.
If you haven't invested in a forklift camera safety solution yet, check out OneTrack’s Warehouse Intelligence platform, which includes everything you need to keep your people safe and productive.
‍
Chapter 1
How to select the best forklift camera system for you
See the benefits of forklift safety cameras and how to select the best technology for your warehouses
‍
Part 2 — Pre-Launch Planning
Set your goals and implementation plan
Once you’ve invested in a good forklift safety solution, it’s time to tackle change management.Â
Typically there’s a couple weeks from when you make the investment to when the forklift cameras actually get installed. And then about 4-6 weeks for what we call the calibration period, making sure that the AI model is tailored to your operations.Â
Don’t let those weeks go to waste. This is the perfect time to map out your goals, start changing processes, and work on a communication plan. Luckily, if you work with OneTrack we’re there to help you every step of the way.
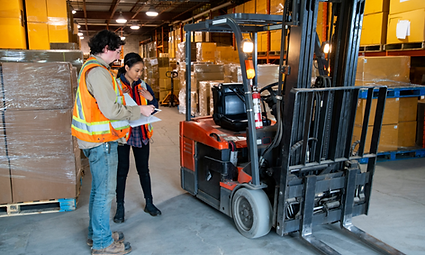
Determine your problem areas
Almost every logistics leader creates a forklift safety program because of a specific problem or pain point.Â
Maybe you’ve had a stretch where accidents are on the rise. Maybe it’s one major forklift accident. Or maybe it’s just a gut feeling that things are happening in your warehouses but you can’t hold operators accountable and coach them.
Whatever that is for you it should become the foundation of your forklift safety program. While the program is sure to grow and expand over time, it’s best to start with a specific problem in mind first.
Set your goals
Now it’s time to set a few goals that you want to achieve from your forklift safety program. Start small here, write down 2-3 specific KPIs that you want to measure and improve.Â
It’s easy to get lost in the data and try and improve everything at once, but that’s a recipe for disaster. You’ll stretch yourself too thin and lose faith in the process.Â
Aim small, miss small. Then scale up.
Common goals for a forklift safety program
- Minimize OSHA TIR
- Reduce unplanned maintenance costs
- Eliminate operator phone useÂ
- Decrease property and product damageÂ
- Improve labor retentionÂ
- Create a culture of safety
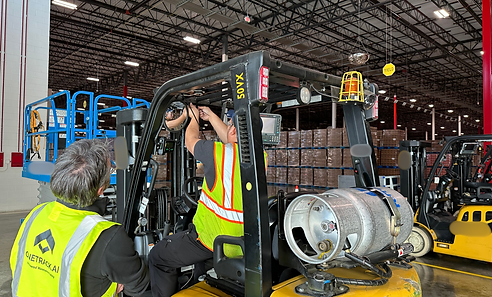
Establish your implementation timeline
Rome wasn’t built in a day and neither will your forklift safety program.Â
Building a solid implementation timeline will help you organize your efforts, align internal stakeholders, and ensure a successful deployment. When building your timeline, make sure to include phases (like “installation, training, and go-live”) as well as key milestones in each phase (like “all supervisors have completed training”).
It may also be helpful to have regular meetings to track progress and stay accountable to your plan, as well as get feedback for ways to improve the overall program.Â
Don’t worry, with OneTrack, our implementation team will help you build this timeline, communicate the plan, and we’ll host regular check-in meetings to keep the project moving.
‍
The phases of a forklift safety implementation
Get everyone on the team on the same page for how things are going to go. This isn’t something that you turn on and magic happens. It takes everyone buying into a new process to foster a safety culture in your warehouses.Â
01. Goal setting
Working with your implementation manager, spend some time on your problems and goals. Even if you don’t know (and it’s okay to not know), try and come up with a hypothesis for the safety problems in your warehouses and how you want to improve them.Â
Think about the specific behaviors you want to coach on (like phone use, distracted driving, or aggressive turning). This is also where you should work on getting the internal team on the same page for the program, timeline, and expectations.
02. Training
OneTrack has created self-guided training modules, a robust knowledge base, and we hold regular check-in calls during this phase. It’s all about getting the team familiar with the system so that when it’s time to go-live, you don’t miss a beat. This is also a good time to start documenting all process changes and expectations.
03. Installation and calibration
While training and goal setting is happening, our Field Services (FSE) Team will schedule an install. We’ll work closely with your team to ensure there’s no downtime or disruption to your day-to-day operations.
Once installed, our engineering team gets to work on calibrating the AI to match up with the specific goals and nuances in your operations. We don’t want to overwhelm your team with alerts, it’s all about showing you what’s important, making improvements, and then scaling up at your pace.
04. Go-live and communication
After calibration is over it’s time to go-live! Our implementation team will have already shared materials to help with this throughout the implementation process, but the biggest thing to focus on here is operator buy-in. There will be some skepticism at first, but across all of our customers, within a month or two it’s operations as usual (except much safer).
05. Stacking value
There’s a lot of data that comes out of a forklift camera safety system like OneTrack. But that’s why we start with a specific goal in mind. Once you’ve gotten used to the system and are seeing results it’s time to do what I call “Stacking value”.
Start stacking on other KPIs, other behaviors, and using reports to really unlock value — but only after you’ve operationalized the basics. Many of our customers start with impacts, phone use, and aggressive driving at first, and then move on to things like productivity, pre-flight inspections, and load validation over time.
‍
‍
Part 3 — Implementation and Rollout
Communicate your forklift safety program and get operator buy-in
The hardest part of any program comes from communication, training, and getting everyone on the same page. Without internal buy-in, no program can succeed, no matter how well planned.
Start with your supervisors
Supervisors need to be involved earlier on in this process than your operators and for good reason. Most warehouse supervisors have never had to coach like this before.
Matt Ireland, Director of EHS at Holman Logistics said, “Supervisors want to stick up for their team. But sometimes that means making excuses for them instead of coaching them. With video evidence, supervisors can’t make excuses for their team members. It helps them grow and be better leaders by holding people accountable.”
‍
3 Tips to Turn your Supervisors into Safety ChampionsÂ
Your forklift safety program success relies on your supervisors becoming safety champions in your warehouses. Here are 3 tips that our customers have found successful.
‍
5 tips to get operator buy-in on forklift cameras
Pushback at the beginning is normal. Change is hard but it’s necessary. To help ensure maximum operator buy-in, here’s some tips that have worked for our customers:Â
‍
01. Set expectations on corrective action
No one wants to be in fear of getting fired. Make it clear what the expectations are for operators and what corrective action will look like.Â
Will you use a “3-strike” policy? Will there be different actions based on different events? Whatever it is, be transparent and consistent so everyone knows what to expect.
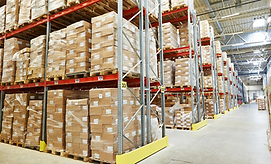
02. Explain how the technology works
Operators’ first thoughts will always go to “Big Brother”. They think someone is sitting in an office watching them work all day. That’s not the case.
OneTrack cameras are monitored by AI. The only way you get a notification is when something goes wrong. OneTrack also collects no biometric data and has no audio recording onboard.
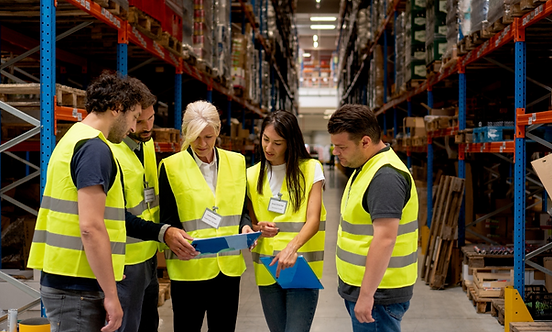
03. Do a soft rollout
Don’t immediately go-live and then try and make an example of someone. Give people a grace period. Set the expectation, but then when you get the alerts, have an informal, off the record conversation.
“We get XX types of alerts now. We saw you doing X and it’s not acceptable. Moving forward, the consequences will be Y.”
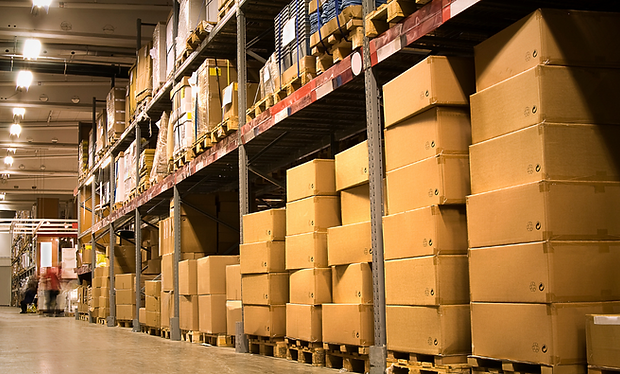
03. Do a soft rollout
Don’t immediately go-live and then try and make an example of someone. Give people a grace period. Set the expectation, but then when you get the alerts, have an informal, off the record conversation.
“We get XX types of alerts now. We saw you doing X and it’s not acceptable. Moving forward, the consequences will be Y.”
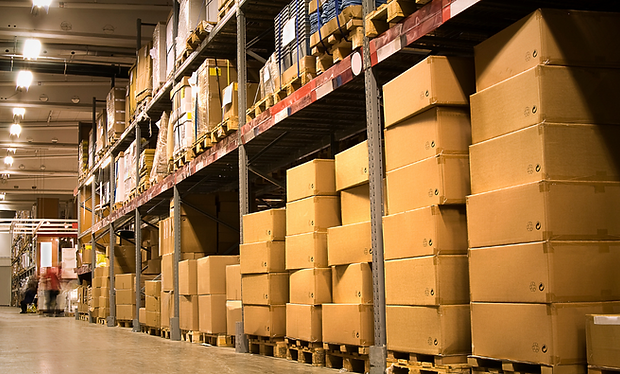
05. Use real video for group coaching
Something we’ve found to be incredibly effective is taking real footage, blurring out operator faces, and then using that during company wide training. It’s a lot easier to connect with something when it’s at your own company, but you're also not making an example out of someone.
‍
‍
Part 4 — Day-to-Day Workflows
Consistent, data-driven, video-based operator coaching
Behavioral coaching is the backbone of any good forklift safety program. Adding data and video takes that to a new level. It’s important to build out consistent coaching workflows to help your team improve operator behavior, reduce forklift incidents, and foster a culture of safety.
Determine your "critical" events
Coaching after serious impacts should always be a priority. But for this, think back to the goals you set. What are the specific behaviors or KPIs you wanted to improve on?Â
Then work with your team to build out a process around that. Want to cut down on operator phone use and not looking in the direction of travel?
Or maybe it's something more specific like unloading rail cars or how operators handle empties.
With OneTrack, your supervisors get real-time email alerts for the safety events that matter to you. This way they can have coaching conversations within minutes of an event happening, when it’s still fresh.
Check out these specific customer examples on how they improved warehouse safety processes using forklift cameras.
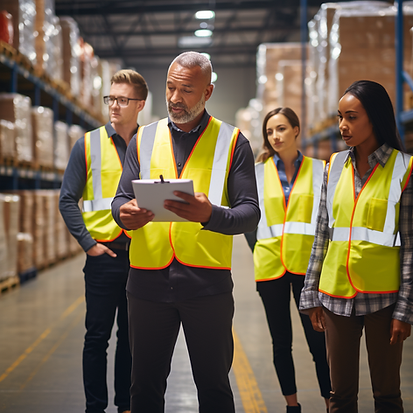
Upgrade your safety meetings with actionable data
Many of our customers hold weekly safety meetings. Their operations managers, warehouse managers, and supervisors all get together, review last week's data, and talk about the coming week's action plan.
OneTrack brings data into that equation. With our reports you can easily get a list of your “riskiest” operators in a given timeframe, quickly see their incident history, and video evidence.
Now during the meeting you can focus on how best to coach these specific operators and talk through ideas to help improve specific behaviors, processes, and root causes in your warehouses.Â
‍
Set-up consistent workflows for corrective action
Should every safety event be sent to operations leadership or should events automatically get assigned directly to supervisors with only critical event types getting escalated?
Some behaviors are worse than others. And sometimes operators simply don’t want to comply with your processes.Â
Either way you can set up automated workflows to loop in operations leadership, or even HR, when a certain trigger is met. Such as an incident that caused serious injury, or a history of non-compliance.
Every warehouse will have a slightly different process. Luckily, a system like OneTrack is completely configurable to meet your specific needs.
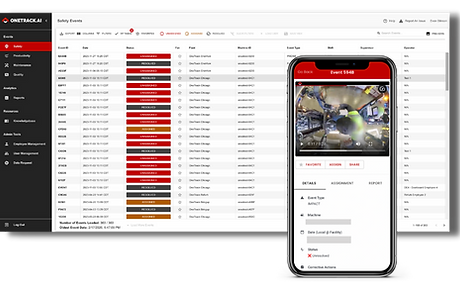
‍
See how OneTrack's coaching tools improve forklift safety
Identify operator coaching opportunities in real-time, and give operators personalized, video-based feedback to improve behaviors.Â
‍
Part 5 — Data-Driven Improvements
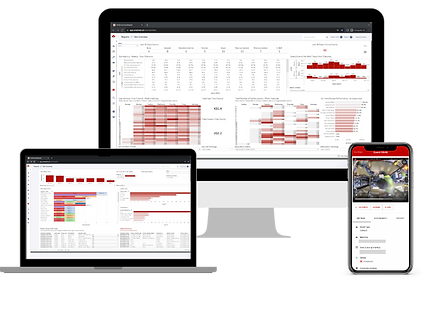
Use robust reporting to make operational process improvements
Video coaching is an incredible piece of your forklift safety program but there’s more to be done.
Warehouses have a lot of data at their disposal, but it’s usually not actionable. Hidden away in 7 different systems and needing complex spreadsheets to do anything with it.Â
With a forklift safety system like OneTrack, you get access to a powerful suite of reporting to make site and network level improvements.Â
From doing a root cause analysis at a site, reviewing network trends, to performing in-depth safety investigations — unlocking your data is the key to a successful forklift safety program.
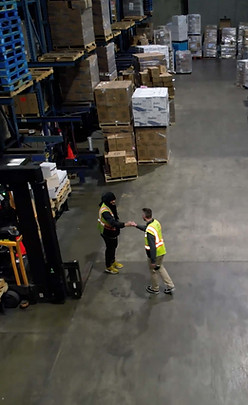
Make forklift safety a priority with OneTrack
OneTrack's AI Forklift cameras and safety tools give logistics leaders the visibility they need to help reduce forklift accidents, improve operator behavior, and lower costs. Explore how our Warehouse Intelligence platform can help you improve safety and drive ROI.
AI Forklift Cameras
Protect your warehouses and keep people safe with AI forklift cameras that monitor MHE for risks 24/7 and send real-time video alerts to help keep operations running smoothly.Â
Dynamic Labor Management
Engineered labor standards are broken. Improve productivity in your warehouses by using AI to proactively alert you of risks, track your labor processes, and connect WMS timestamps with video context to make critical process improvements.Â
Proactive Operator Coaching
Coaching shouldn't ONLY happen after a major incident. Get alerts of the leading indicators of MHE safety incidents to coach operator behavior proactively and change the culture in your warehouses.Â
‍
‍
Chapter 3: Capture ROI from Your Forklift Safety Program
‍
How do you quantify the ROI of a safer warehouse?
Investing in a video-based forklift safety program isn’t just about making sure your operators clock out in the same condition they came to work in — it’s also a great way to save money. From reducing forklift accidents costs to avoiding false workers comp claims, read on to learn how to measure the value of your forklift safety program.
Results from OneTrack customers
- 15%+ lower labor cost per unit
- 75%+ lower OSHA TIR
- 56%+ fewer product damages
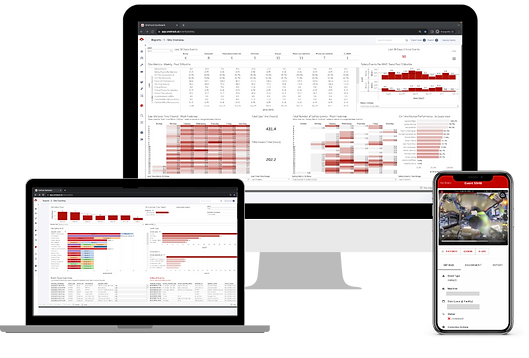
Something BIG Is Happening 4/17 That'll Change Warehousing For Years To ComeÂ
‍
In this chapter:
01. Reduce forklift accidents: Decrease the frequency and severity of forklift impacts in your warehouses
02. Decrease unplanned maintenance: Minimize wear and tear to extend the life of your MHE fleet
03. Avoid false workers comp claims: Use video evidence to upgrade safety investigations and avoid unnecessary payouts
04. Retain and upskill operators: Foster a safety culture to improve morale, reduce turnover, and upskill forklift operatorsÂ
05. Optimize labor costs: Unlock productivity gains through idle time alerts, less MHE downtime, and reduce indirect time

 CUSTOMER STORYÂ
93% reduction in overall safety events
73% reduction in forklift impacts
‍
Part 1 — Reduce Forklift Accidents
Decrease the frequency and severity of forklift impacts
Probably the most important benefit that can come from a successful video-based forklift safety program is a decrease in forklift accidents in your warehouses. While it’s tough to say “all forklift impacts = $X”, there are a few things to look at in terms of ROI.Â
How does a successful forklift safety program reduce accidents?
The best forklift safety programs combine two key things: Video based coaching and actionable data. Together, they give you the deep visibility that you need to coach operator behavior, improve safety processes, and reduce forklift accidents in your warehouses.
OneTrack customers see a 77% decrease (on average) in forklift impacts after implementing a forklift camera system and coaching their operators.Â
Plus as you continue to coach on the leading indicators in your building, you will proactively get ahead of incidents and should see dramatic improvements over time.
Want to see for yourself how OneTrack works? Check out this interactive product tour.Â
‍
When and how to measure ROI
Across the board, OneTrack customers see a dramatic drop in forklift impacts within 3-6 months of going live. As you continue to consistently coach operators, you’ll see a noticeable drop in both frequency and severity on forklift accidents.
If you aren’t using a system with built in analytics like OneTrack, we recommend keeping a tally of impacts in a spreadsheet, both before and after you go live with a system. This way you can calculate the percent drop in the number of accidents and associated costs.
If you’re a OneTrack user, you can take a look at your safety dashboards to see your impact trends at a specific site or across your network. It’s also a good idea to take a look at soft impacts, aggressive driving, and product hits as well to get an overall picture. Of course, with less serious accidents you’ll get less accident related costs.
Key performance indicatorsÂ

Decrease in forklift impacts

Decrease in accident related costs

Decrease in overall safety events

Decrease in product damage

Decrease in "critical" events
‍
Part 2 — Decrease Unplanned Maintenance
Minimize wear and tear and extend the life of your MHE fleet
It’s not just the serious impacts that can impact your bottom line, it’s also the small impacts, bumps, and scratches. This wear and tear adds up over time and can be a “budget buster” when it comes to maintenance above and beyond your plan.Â
‍
How a successful forklift safety program reduces unplanned maintenance costsÂ
Luckily, with a forklift camera system you can coach operators and start eliminating these smaller safety events and extend the life of your MHE.Â
Behaviors like not looking before reversing and bumping racking, unsafe dock plate maneuvers (can damage your tires), and small hits to other MHE can add up to cost a fortune in maintenance expenses.Â
But by getting real-time alerts of these behaviors, your supervisor team can have coaching conversations with minutes of these events happening. And while these don’t require formal corrective action, that increased accountability will start to work it’s way into the culture of your warehouses.
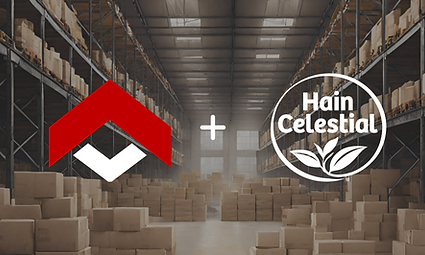
 CUSTOMER STORYÂ
80% reduction in overall safety events
70% reduction in forklift impacts
‍
When and how to measure ROI
Long story short, with a good forklift safety system and program, you’ll see an almost immediate reduction in things like phone use, not looking in the direction of travel, and small impacts. However, you should wait at least a few months before pulling maintenance cost data to get a good picture of your savings.Â
Most logistics leaders track their overall maintenance budget in a spreadsheet and then keep track of any unplanned expenses. Keep an eye on that change over time while also documenting the change in unsafe behaviors.Â
With OneTrack, it's simple to keep track of your safety trends. You can easily see how that change is affecting your maintenance costs. You may even be able to push out fleet replacements by months (or years!) which can mean massive savings.
‍
Key performance indicatorsÂ

Extended fleet replacements and lease extensionsÂ

Reduction in unplanned maintenance spendÂ

Decrease in "leading indicator behavior

Decrease in rack damage
‍
Part 3 — Avoid False Workers Comp Claims
‍
Use video evidence to upgrade safety investigations and avoid unnecessary payoutsÂ
Death, taxes, and workers comp claims. An unfortunate reality, no matter how good your forklift safety program is, accidents will inevitably happen. And with that, comes the risk of paying out false claims.Â
‍
How forklift camera systems can reduce false claim payouts
The good thing about workers comp claims is that you don’t actually make the decision to deny or pay. All you do is conduct an investigation and provide evidence.Â
Traditionally when a workers comp claim comes in, you’d start by interviewing employees who may have been in the area, and potentially watching back through your CCTV footage to try and get a view of what happened. Unfortunately, CCTV doesn’t always catch everything, isn’t always a great viewpoint, and is always a time consuming, manual process.Â
With a forklift camera system, like OneTrack, it streamlines this process in two key ways. For starters, you’ll likely have gotten an alert of the safety event if it really happened, eliminating the need to go hunt through CCTV. Second, you can actually request footage during a certain timeframe to get extra viewpoints if you think a piece of MHE was in the area.
This collection of video evidence is concrete, (mostly) automated, and has saved our customers hundreds of thousands of dollars in unnecessary payouts.
‍
When and how to measure ROI
It’s hard to put a timeframe on this. Some years you may have 0 claims to contend with. Other years you could deal with multiple.Â
Doing this on a case by case basis makes the most sense. After a claim comes through that turns out to be false, make sure to follow up and take note of the potential payout if the decision went the other way.Â
Keep a running list of these amounts, and during your quarterly — or yearly — safety reports, be sure to include that hard dollar figure as savings associated with your forklift camera investment.
‍
Key performance indicatorsÂ

Dollars saved on false payouts

Decrease in number of false claim payouts
‍
Part 4 — Retain and Upskill Operators
Foster a safety culture to improve morale, reduce turnover, and upskill forklift operators
Any other logistics leaders feel like they’re constantly battling turnover in your warehouses? You aren’t alone. We’ve heard stories on hiring a warehouse worker and then by lunch time that person is already gone. And with it costing 25% of an operators salary to replace them, turnover costs can get out of hand quickly.
How a successful forklift safety program increase retention?
It might sound counterintuitive at first, given the initial operator push back to forklift cameras, but these safety systems actually help to decrease operator turnover, improve onboarding efforts, and upskill your existing operators over time.Â
It may take a few months, but eventually your operators will understand that the forklift camera system is there to help keep them safe. All it takes is consistent communication and coaching and they’ll buy-in to the process. Plus, when you bring in new operators, that’s all they know, so it makes for smooth onboarding. That kind of culture change helps to attract talent, retain your top operators, and through consistent coaching, you’ll see a noticeable increase in operator performance.
When and how to measure ROI
With the labor shortage seemingly a part of every headline these days, keeping track of operator retention is critical. It’s best to wait until 3-6 months after you’ve introduced a forklift camera system to your safety program to give operators a chance to get used to the system and buy-in. It’s also a good idea to collaborate with your peers in HR to keep a pulse on turnover costs and recruitment savings.Â
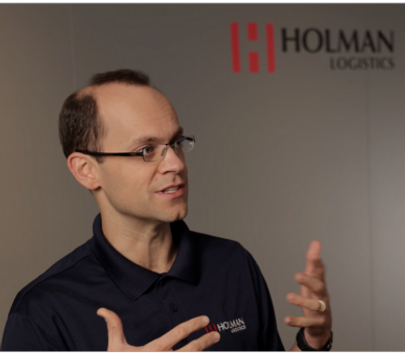
Holman Logistics
‍OneTrack is an integral partner for us. We've got OneTrack tools that help us to keep our people safe. OneTrack enables us to be smarter in how we do labor planning, how we do safety analysis, and in how we do building utilization.”
Brien DowniePresidentRead Case Study
Key performance indicatorsÂ

Dollars saved on recruitment and replacement

Decrease in operator turnover

Increased onboarding speed
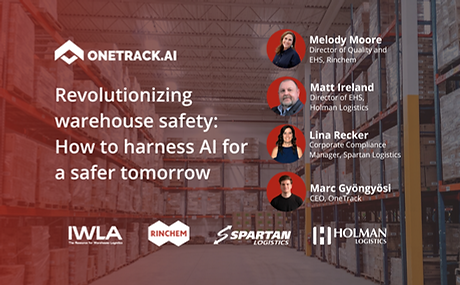
‍
See how 3 logistics companies use OneTrack to keep people safe
Hear real stories from real logistics leaders about their experience using AI forklift camera systems to keep their people safe and productive.
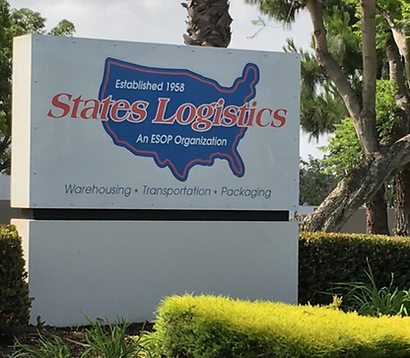
 CUSTOMER STORYÂ
72% reduction in overall safety events
‍
Part 5 — Optimize Labor Costs
Increase productivity through idle-time alerts, less MHE downtime, and AI-labor managementÂ
Almost every logistics leader we talk to mentions they plan to reduce costs, and a major piece of that plan is to optimize their labor costs. But how do you actually do that and how does it tie into your forklift safety program?Â
How your forklift camera system can help optimize labor costs
This is where things get really interesting. Keeping people safe is priority number 1 for every logistics leader, but once you get a good handle on your forklift safety program there are a lot of benefits that a forklift camera system can bring you.Â
For example, with OneTrack we offer an entire AI labor management suite that helps you track forklift idle time, gap times around shift changes, and around long running lunches or breaks.
It can also integrate with your WMS to combine timestamp data with video evidence so you can actually see why certain processes or picks are taking longer and make improvements instead of having to hunt through an excel sheet.
‍
When and how to measure ROI
Typically our customers start with safety. It’s the easiest thing to influence right away. But after about 6-12 months of using the system, they start to use other functionality.
The great thing about OneTrack is that all features are included in your subscription, no upsells. It’s just a matter of when you decide to use it all
We’ve built out productivity dashboards that will show you how much time you might be losing to gap time, idle time, indirect time and poor processes and what the labor spend is related to that so you can easily show and report on success.Â
Key performance indicatorsÂ

Decrease in indirect labor spendÂ

Decrease in forklift idle time

Decrease in "lost time"
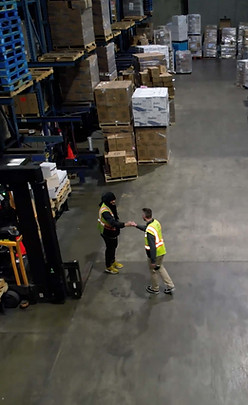
Make forklift safety a priority with OneTrack
OneTrack's AI Forklift cameras and safety tools give logistics leaders the visibility they need to help reduce forklift accidents, improve operator behavior, and lower costs. Explore how our Warehouse Intelligence platform can help you improve safety and drive ROI.
AI Forklift Cameras
Protect your warehouses and keep people safe with AI forklift cameras that monitor MHE for risks 24/7 and send real-time video alerts to help keep operations running smoothly.Â
Dynamic Labor Management
Engineered labor standards are broken. Improve productivity in your warehouses by using AI to proactively alert you of risks, track your labor processes, and connect WMS timestamps with video context to make critical process improvements.Â
Proactive Operator Coaching
Coaching shouldn't ONLY happen after a major incident. Get alerts of the leading indicators of MHE safety incidents to coach operator behavior proactively and change the culture in your warehouses.Â