Take the Blindfold Off Your Warehouse Operation
Great operators aren’t found anymore, they’re made — through consistent coaching and rock solid processes.
But to do that you need a way to easily see:
- Who your best and worst operators are in terms of safety, productivity, and quality
- How operators are trending with specific events like phone use, impacts, and idle time
- If your coaching efforts are making a difference with an operator or if further escalation is required
Here’s a step-by-step playbook showing how you can take a data-driven approach to employee coaching and turn your riskiest operators into top performers.
Let’s break it down.
Or you can take this interactive safety tour to see how OneTrack works for yourself.
How it works
Identify who your riskiest operators are
Drill into their scorecards to better understand their overall performance
Watch event footage to find coaching opportunities
Work with supervisors and team leads on an action plan for improvement
Determine next steps if there are no signs of improvement
The Playbook
Step 1: Identify who your riskiest operators are
Every employee is bound to make a mistake every once in a while.
OneTrack makes it easy to coach operators right after a mistake happens with real-time video alerts after an incident.
But to make big strides toward an incident free warehouse, you need a program focused on your “riskiest” operators.
You probably have an idea who falls into this category, but it’s best to take a systematic, data-driven approach. That way, no one can accuse anyone of being unfair or being targeted.
To do that, we’re going to jump into the OneTrack Platform > Reports > Click to Load a Report > LSW > Site Coaching.

As soon as you land on the Site Coaching dashboard, you’re going to want to adjust your timeframe and plant to reflect what you want to see. For example, I want to look at XYZ Palm Springs for the last 8 weeks.

Now that we have the right filters set, we really want to look at one key part of this dashboard, the most help needed (MHN) report.
If you want a full breakdown of how to use this dashboard and others to measure your overall safety program performance, take a look at this playbook.

The MHN report is going to show all of the operators in your facility, ranked by their incident history.
You’ll be able to see which operators have the most total events (in safety and productivity), or you can filter only by event type to see which operators are involved in the most impacts, use their phone the most, or frequently take long lunches for example.
You can adjust these filters depending on what behaviors you’re looking to improve — safety, productivity, or a mixture of both.
I’m just going to look at safety for my operators, so I’ll select the following review types:

- Aggressive turn
- Bump
- Dockplate
- Forkmast
- Impact
- Phone use violation
- Safety Coaching (This would be leading indicators like not looking in the direction of travel)
This will change for every warehouse, but for simplicity sake I'm going to take note of my top 5 riskiest operators, since there’s a significant drop off in the number of safety events after that in this warehouse.
Step 2: Drill into operator performance with the employee scorecard
With those operators identified, I’m now going to jump to another LSW dashboard: Employee Scorecard.
As soon as I land, I'll filter by my plant, XYZ Palm Springs, make sure my timeframe is set to 8 weeks, and select the first operator on my list, Operator Fli.

Now I can see a few things:

- How many critical events (caused damage or injury) this operator was involved in
- A list of event types this operator was involved in
- Supervisor statements and links to the footage of each event
- Opportunity time and productivity events
(This is just a sample dataset, over 8 weeks it’s likely that your riskiest operators will have more than 3 events.)
I also like looking at the supervisor statements and review descriptions to ensure that proper coaching happens after each event, but nothing beats seeing it firsthand.
Let’s dive into some of the footage and see what coaching opportunities or process improvements we can find.
Step 3: Watch event footage to find coaching opportunities
On the employee scorecard dashboard, I can quickly jump straight into the footage from each event.

I feel pretty good about how my supervisors are coaching on phone violations, so I'll stick to reviewing impacts and critical events. Here are a few examples of what I found:
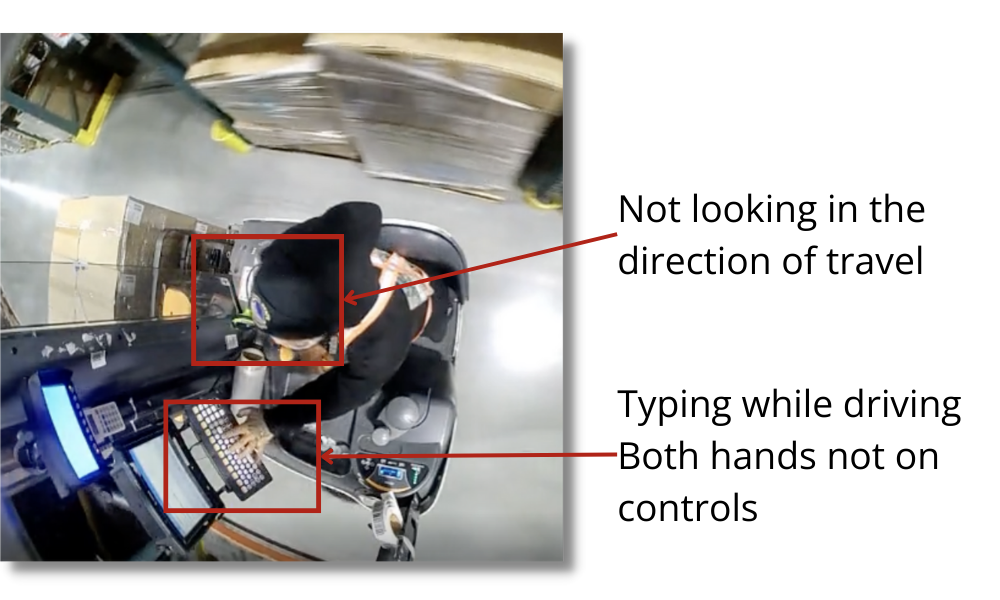
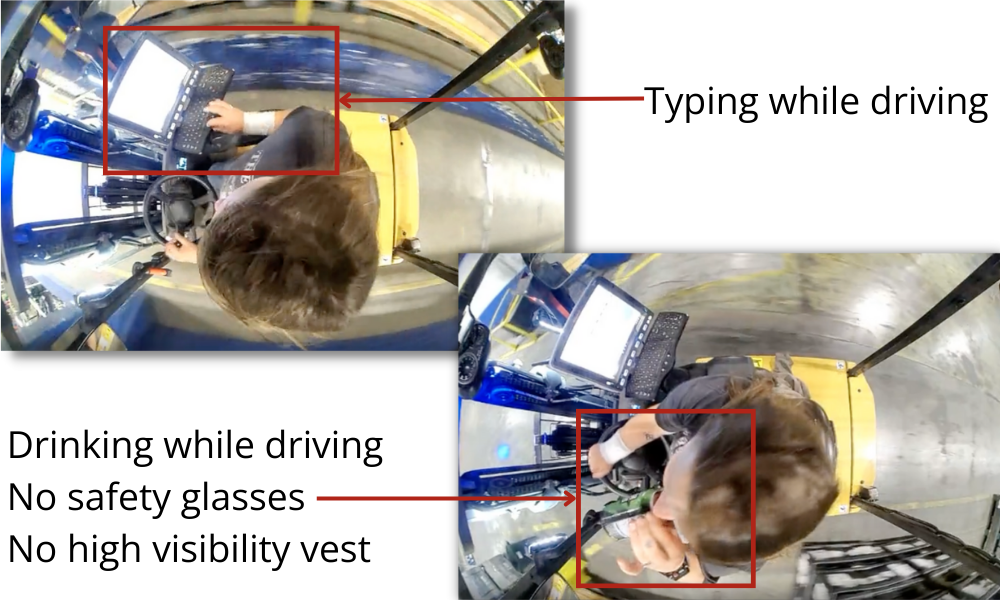
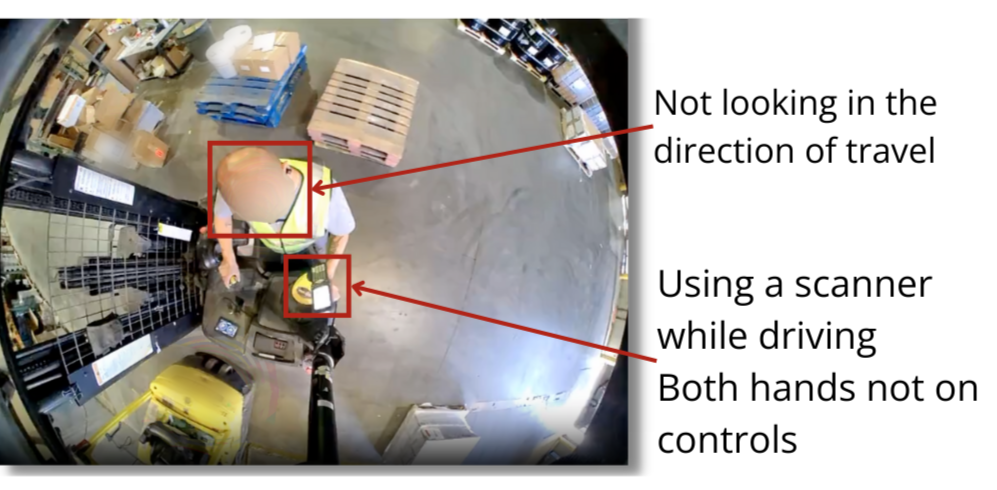
There are always coaching opportunities after an impact, but the impact itself can sometimes hide the behaviors that led to it.
It’s easy to tell someone to be more aware of their surroundings, but what about things like:
- Wearing a hood while driving (restricts peripheral vision)
- Wearing air pods (can’t hear the horn, people talking, and can be distracting)
- Not looking in the direction of travel, typing while driving, or using a phone
- Not using the horn at an intersection
- Not being fully strapped in to the equipment (depending on your processes)
- And countless others.
Bottom-line is that it’s crucial to watch the video footage with a critical eye. What really went wrong? What could be improved?
That’s how you change behaviors and foster a culture of safety in your warehouses.
Step 4: Work with supervisors and team leads on an action plan for improvement
Lasting behavior change doesn’t happen overnight — at least not for your riskiest operators.. It takes consistent coaching. And for that, I need to come up with an action plan with my supervisors and team leads.
What many customers — like Hain Celestial — do is use that LSW site coaching dashboard, specifically the MHN report, during daily or weekly safety meetings. Any operator in their top 5 or 10 in terms of incidents that week, they specifically dig into their events, and discuss what the coaching plan will be.
This keeps everyone aligned on corrective action and coaching, while bringing some data-driven focus to your regular meetings.
If you don’t see an operator from your original list come up in a given week, that’s a good thing!
You can hop over to their employee scorecard for more details — and if you string together a few weeks of minimal safety incidents then you’re well on your way to turning your riskiest operators into top performers.
Step 5: Determine next steps if there are no signs of improvement
I’d like to be able to say that every operator will respond to coaching. Most will — but there are always going to be a select few that don't want to comply with your processes (and puts everyone around them at risk because of it).
When that situation comes around, you want to be prepared. The process looks different at every company in terms of corrective action, but here’s a piece of advice every company should follow:
Take the emotion out of it. Set a standard. Escalate as needed.
With OneTrack it’s easy to set a process and hold people accountable to a standard using data.
We do that by setting up automatic notification triggers so that the right people, get the right information, at the right time.
A “critical event” happens in the building? An instant notification can go to the general manager.
If an operator is involved in 3 impacts within 5 days? An email can get sent directly to Operations and EHS leadership to see what’s causing the accelerated impact numbers.
If an operator has been in your top 5 MHN report for 3 months straight? HR can get an automatic alert to begin a formalized corrective action plan.
No need to put together paperwork or find enough time in the day to march down the hall to HR — they're automatically looped in based on a process that you pre-defined.
Want to put this playbook to work for yourself?
This playbook will help you make massive improvements to your warehouse safety, turning your riskiest operators into safety champions.
In just a few minutes you now have data on:
- Who your riskiest operators are in terms of safety, productivity, or specific event types
- A full breakdown of their overall performance, all wrapped up in an employee scorecard
- Video coaching opportunities for your specific operators
- A way to keep everyone aligned on coaching and corrective action
- A process set up to automatically loop in cross-functional stakeholders to assist with corrective action
That’s what Warehouse Intelligence is all about.
One platform to easily view how your warehouses are performing with safety, drill into individual operator performance, and develop an action plan to turn your riskiest operators into top performers.
Want to put this kind of data to work in your warehouses?
OneTrack customers, good news! You already have this at your fingertips. Reach out to your implementation manager or support team with any questions.
If you aren’t a OneTrack customer, book a custom demo here. We’ll connect to better understand your operations and show you what a partnership could look like.