Take the Blindfold Off Your Warehouse Operation
Take a look at (almost) any warehouse’s budget and you’ll see a number with a lot of 0’s going toward their MHE fleet.
Most warehouses could save thousands — if not tens of thousands — of dollars on their forklift fleet each year. But it’s not a simple task without the right data and visibility.
We’re going to walk through, step-by-step, how OneTrack customers are getting visibility into their forklift fleet utilization, usage, and processes to answer the most critical questions about their fleet and ultimately save money.
Let’s dive into it.
How it works
Get a bird's eye view of your forklift fleet utilization by day and by hour
Drill into your lift usage to see your equipment with high idle time
Uncover which processes are causing the most idle time
Bonus step: Get an overall network view of your MHE fleet
The Playbook
Step 1: Get a bird's eye view of your forklift fleet utilization
Before you can adjust lease terms, your processes, or right size your fleet you have to be able to answer one question.
“Are all my lifts actually getting used?”
OneTrack makes it an easy question to answer. Just hop over to the OneTrack Platform > Reports > Click to Load a Report > Drive Metrics > Â Equipment Utilization.
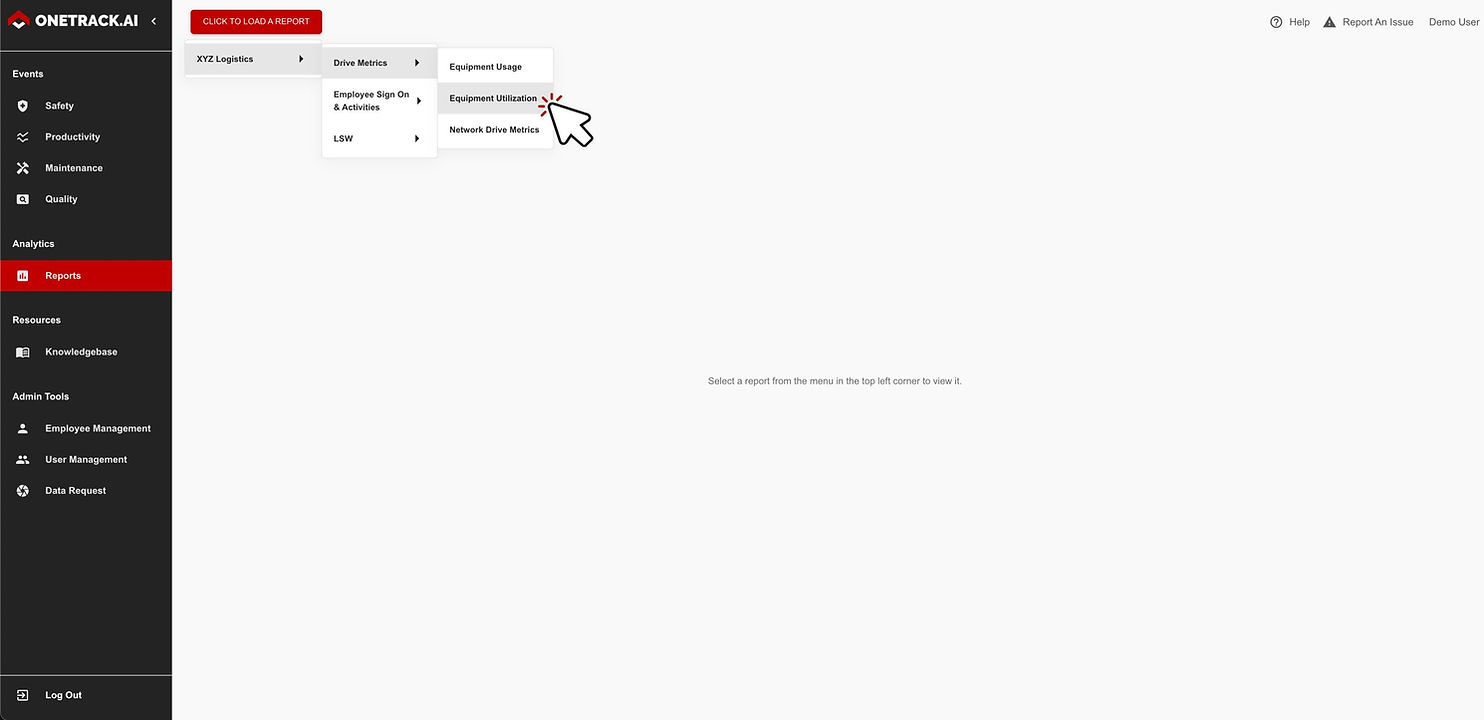
You can use this dashboard to easily see your fleets forklift utilization by specific sites, or across your entire network.
I want to focus on my fleet at the Raleigh site today.
Right off the bat you’ll see a couple things:
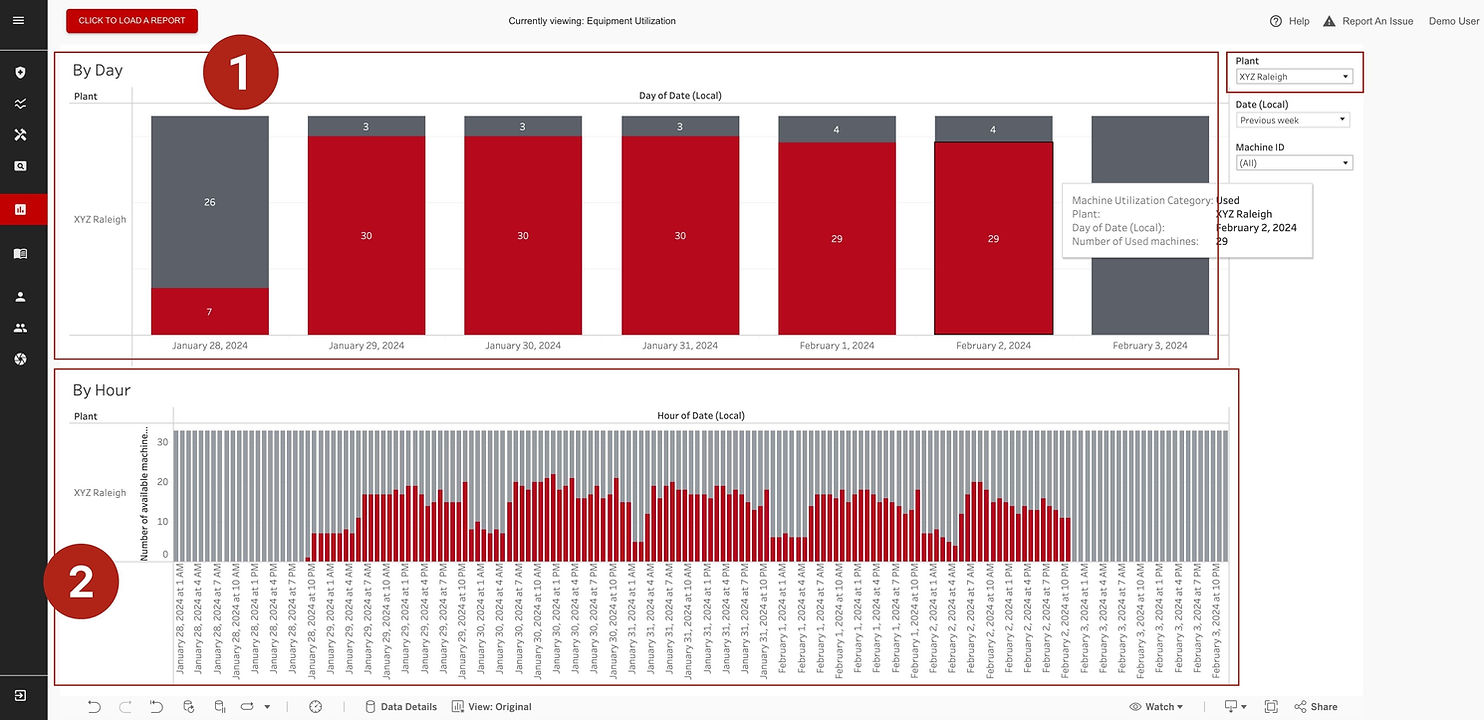
- How many lifts per day aren’t getting utilized
- Utilization by hour for the week
By clicking on a specific day you can see a breakdown of utilization by hour, for the lifts that were actually used for that day.
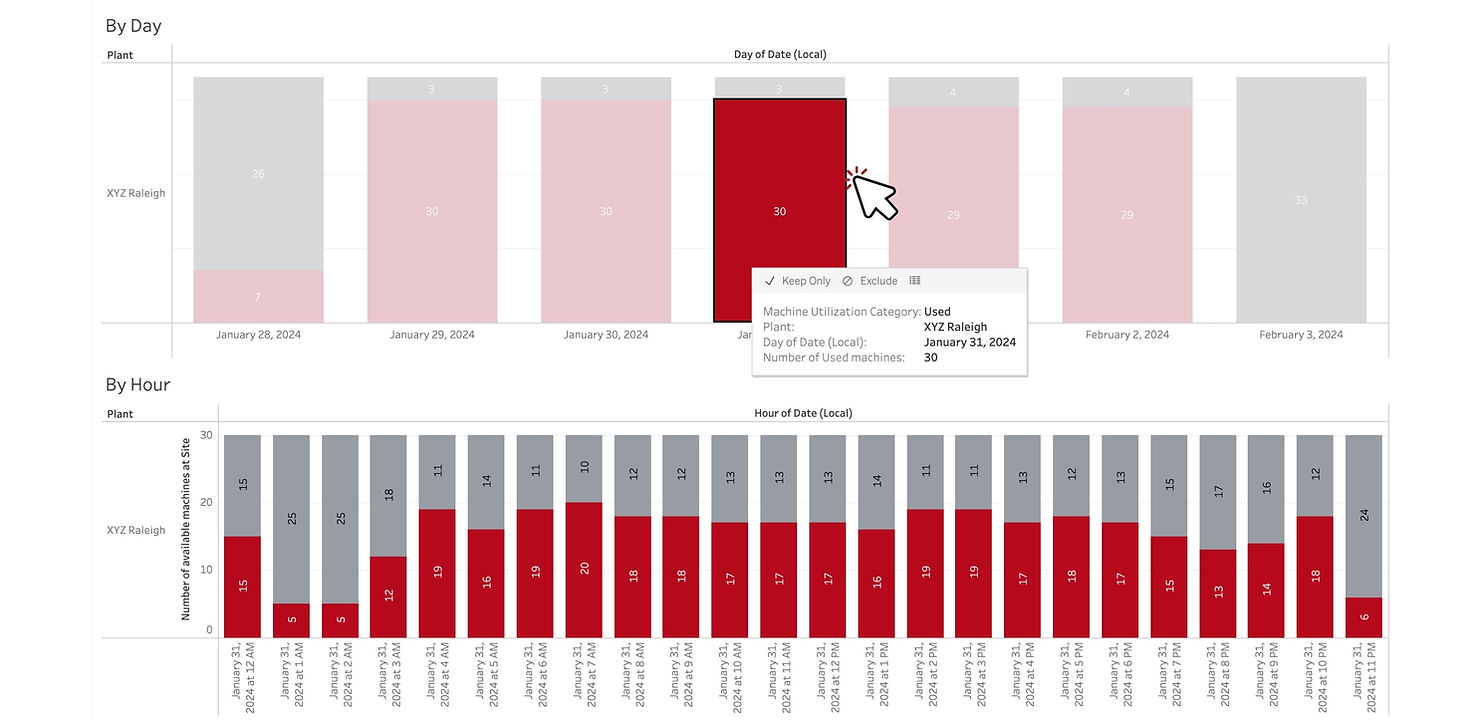
For this site, I can see that I never actually use more than 20 pieces of MHE at a given time, plus the 3 lifts that didn’t get used at all for that day. Every site should have a few extra around in case of maintenance, but 13 seems excessive.
That’s one quick area I might be able to save some costs by right sizing my fleet or moving equipment to another facility.
Step 2: Drill into lift usage to understand forklift idle time
Now let’s go a little deeper and see what else we can find.
Hop over to Reports > Click to Load a Report > Drive Metrics > Â Equipment Usage.
I’ll change my filter to my Raleigh site to keep things consistent.
This dashboard has two main sections, but there's a ton you can do with this data.
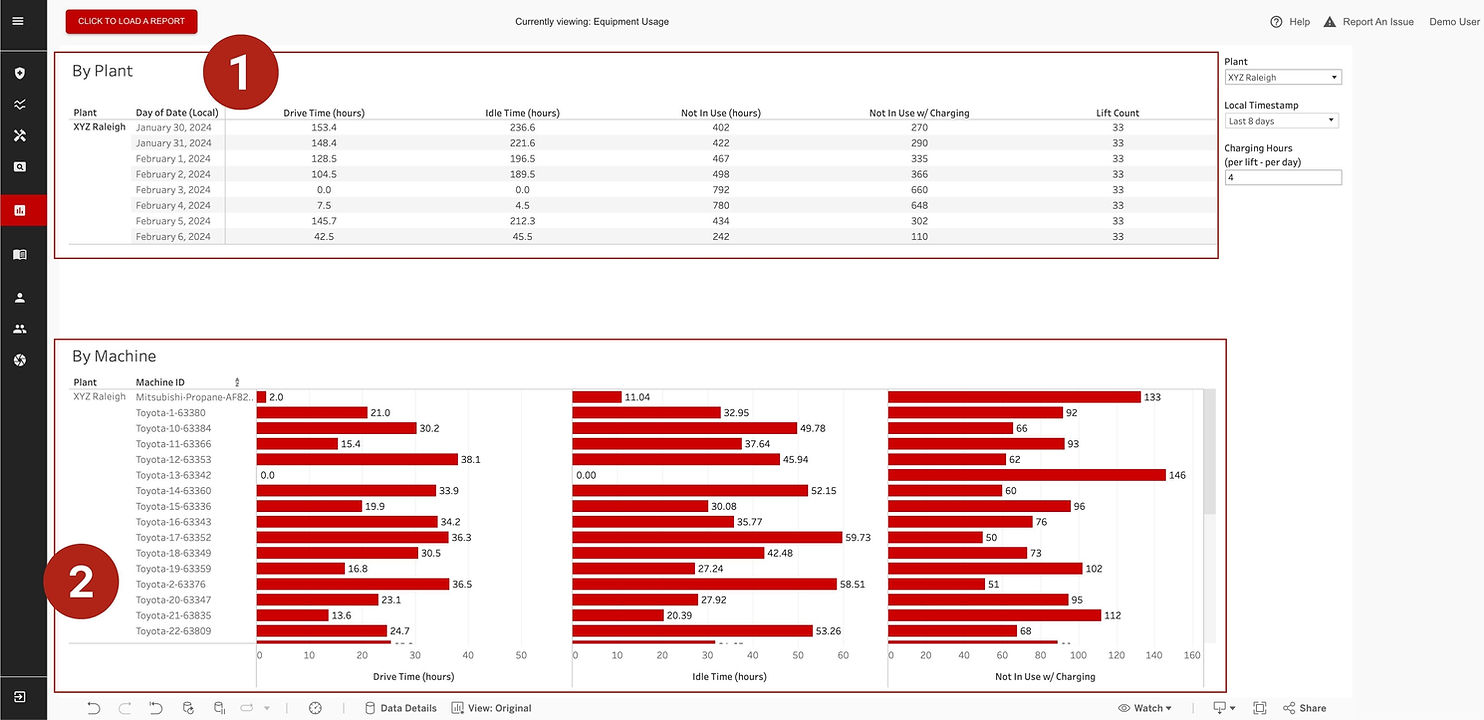
- An overview by plant (in this case we’re just looking at Raleigh), broken down by drive time, idle time, and not in use time.
- A drill down by machine broken down by drive time, idle time, and not in use time.
First let’s define what we mean by drive time, idle time, and not in use — and then I'll tell you my favorite thing about this dashboard.
Drive time: The lift is actively being driven around your facility
​
Idle time: The lift is in operation BUT is just sitting still. Maybe the driver is on their phone, maybe they’re waiting on paperwork, could be a spill clean-up. But the lift is idling and not being productive.
​
Not in use: No one is operating the MHE. We show you how much of this time is spent charging as well as total not in use time.
Looking at the overall breakdown by plant (and day) is interesting. At a glance you see anything that may standout. Maybe it’s excessive idle time or not in use time that you need to dig into.
But my favorite part is looking at “By Machine” and then doing some filtering to rank by drive time and idle time.
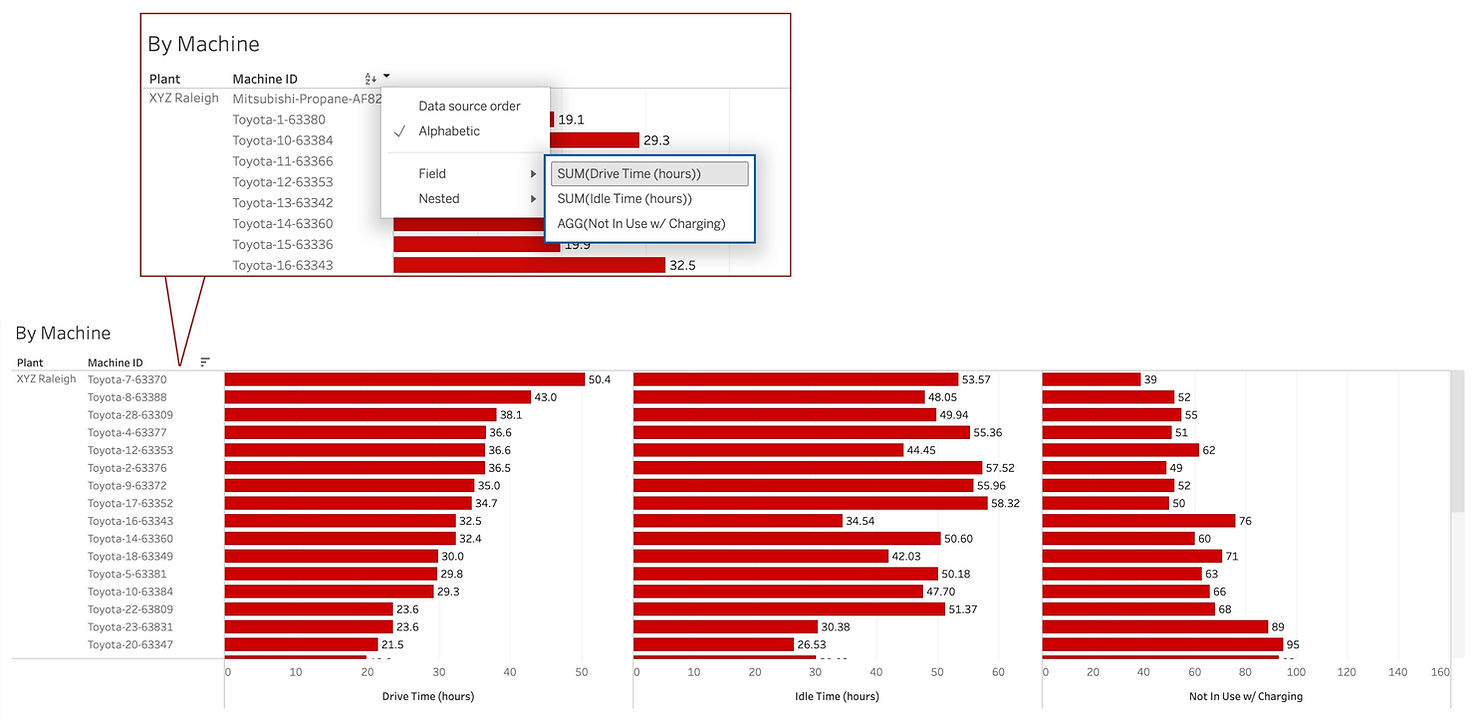
You can easily see what pieces of equipment are driven the most (or least).
For example if you have a specific type that’s being driven way more, you can start digging into why. Do you actually need more of that type of lift in your facility? If it’s driven more it’s going to need maintenance sooner than the rest of the fleet.
If there are types driven much less, is it a specialized piece of equipment or is it something else? Maybe operators rarely need to use a certain type of lift because you have more than you really need.
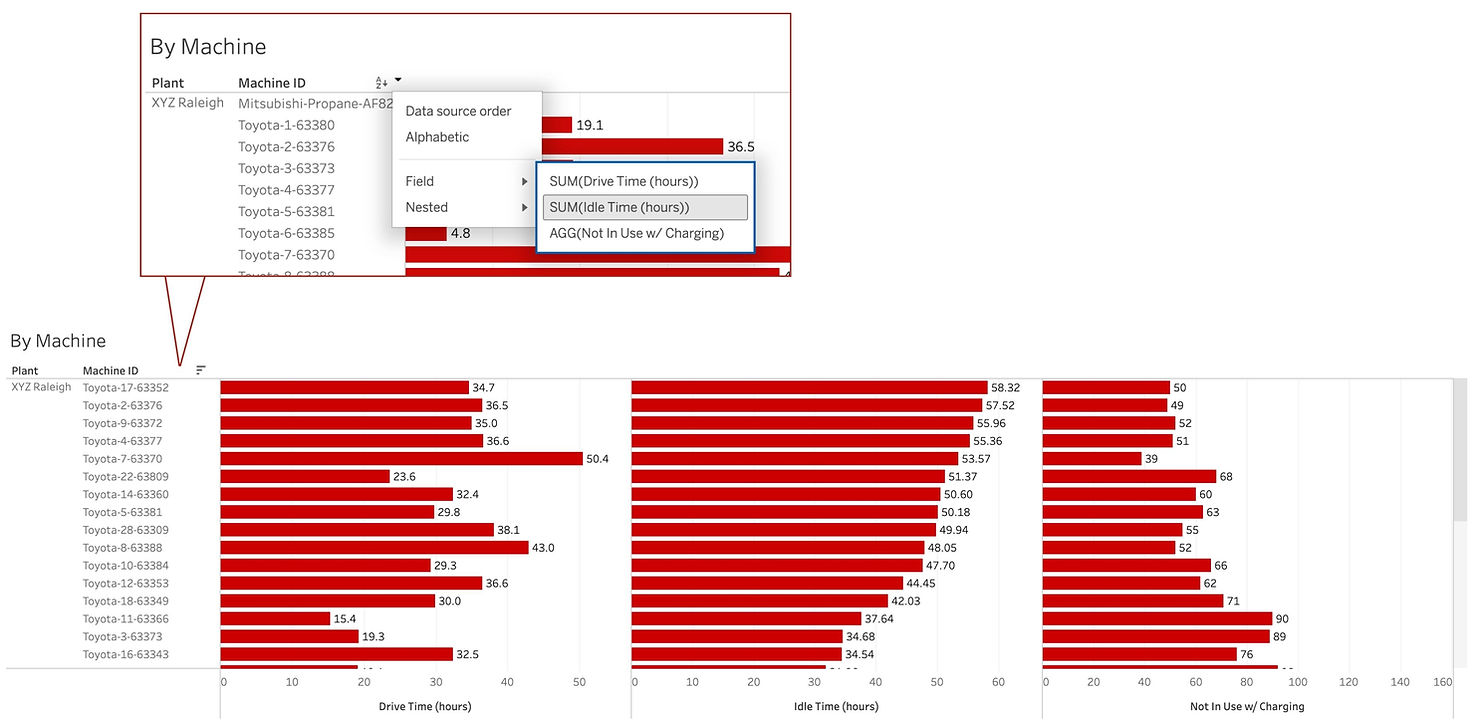
I find this interesting for two reasons.
- If I filter and see a trend in high idle time on a certain type of equipment, that usually signals a process impediment.
- If there’s a trend for low idle time, I can investigate why and replicate it. Maybe it’s a well oiled process that I can mirror in other places.
Step 3: Perform a root cause analysis (RCA) for your network
I noticed a trend of high idle time on a certain type of equipment. But I still don’t know why. Let’s change that.
OneTrack gives you the ability to track your indirect processes — things your WMS or LMS can’t.
Activities like waiting on paperwork, battery changes, cleaning up spills, unloading mixed freight… really any process in your warehouse that you want to start tracking, you can.
To dive into this data, go over to Reports > Employee Sign-on & Activities > Employee Activities.
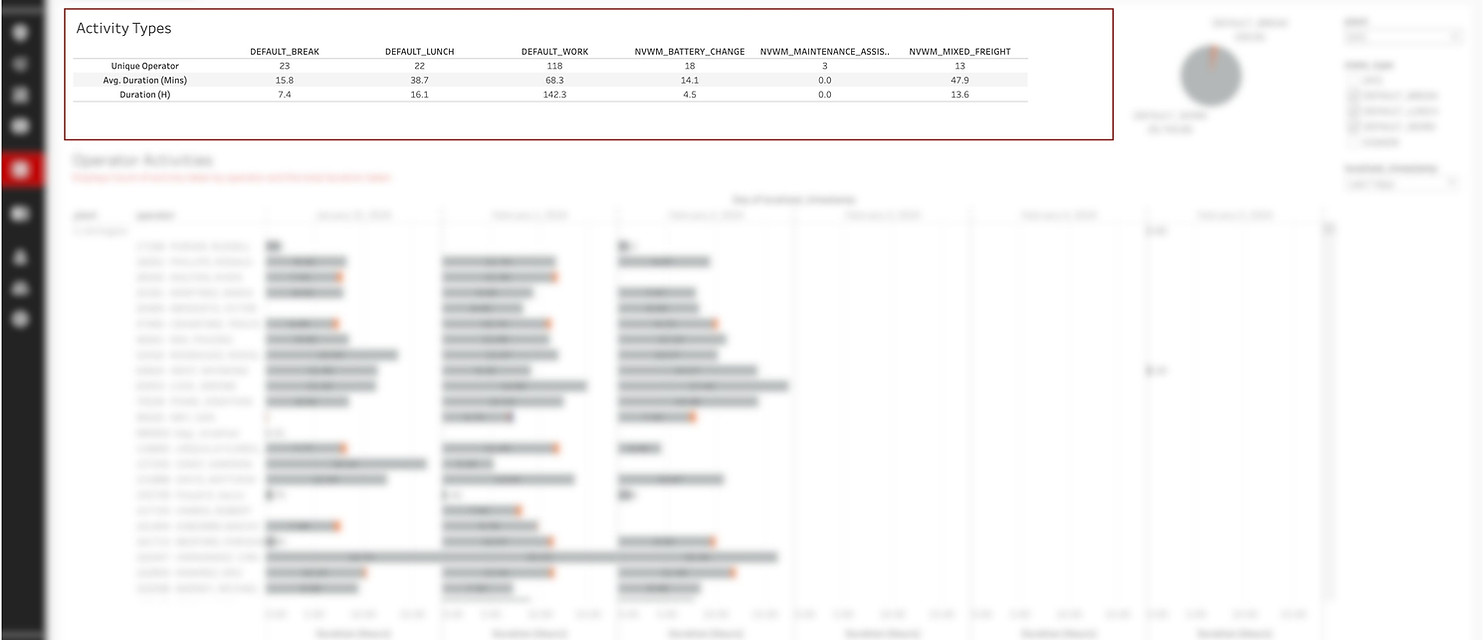
This is going to show you an overview of operators at a site, plus a look at their activities throughout the day. I’ll just focus on the overview, but you can get as granular as you need in looking for specific process breakdowns.
Want a playbook for digging into your processes and indirect time to optimize labor costs and boost throughput? Check it out.
For investigating idle time, I see that a lot of time is being spent unloading mixed freight and a decent chunk of time is being spent waiting on battery changes.
With that data, I’m going to figure out how to reallocate labor resources more efficiently to meet demand around mixed freight.
And I can either make adjustments to our battery change process so operators aren’t waiting around — or it could be a signal that I actually need more of a certain type of lift so there’s more options when one goes in for maintenance.
If nothing stands out on this dashboard I highly recommend checking out your phone violations to see if there was a spike that’s causing more idle time. Or it could be a process impediment that you aren’t currently tracking.
Bonus step: Get an overall network view of your MHE fleet
We focused mainly on tracking your MHE fleet at a specific site, but what about if you want a good view of multiple sites?
Good news — any of the dashboards we already looked at let you see multiple sites at a time, but we haven’t looked at my favorite network level MHE dashboard yet.
Let’s take a look at the Network Drive Metrics Dashboard.
This dashboard shows you:
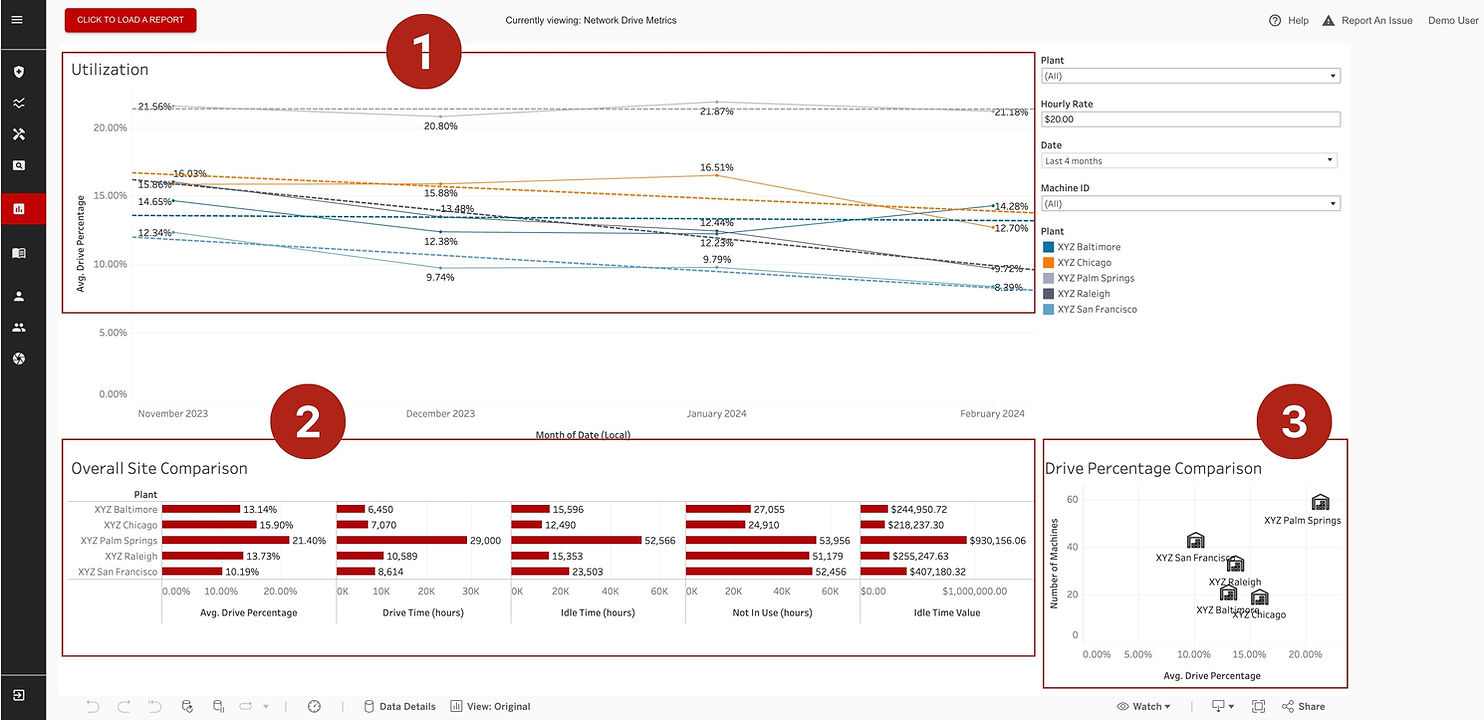
- Average forklift utilization across multiple sites or your entire network
- Site comparison on drive time, idle time, not in use, and even shows you how much money you’re losing to idle time
- A comparison graph showing how utilization while taking into account the # of MHE
This is a great bird’s eye view to spot any outliers across your MHE network. In this case I see that my Palm Springs site has the best lift utilization while San Francisco has the worst.
Now I can investigate accordingly.
Want to put this playbook to work for yourself?
This playbook gives you the visibility you need to answer critical MHE questions to run your fleet efficiently, effectively — and save money in the process.
In just a few minutes you now have data on:
- Your MHE utilization at a site
- A breakdown of drive time, idle time, and not in use time
- Which types or pieces of equipment are used the most, least, and have the most idle time
- What indirect processes may be a driving factor of increased idle time
- An overview of your entire MHE fleet
Now that’s what Warehouse Intelligence is all about.
​
Want to put this kind of data to work in your warehouses?
OneTrack customers, good news! You already have this at your fingertips. Reach out to your implementation manager or support team with any questions.
If you aren’t a OneTrack customer, book a custom demo here. We’ll connect to better understand your operations and show you what a partnership could look like.
‍