Take the Blindfold Off Your Warehouse Operation
PLAYBOOK
How to eliminate idle time and optimize labor spend without a WMS or LMS
Every logistics leader is talking about ways to reduce costs.
One of the best (and easiest) that we’ve seen is to focus on your processes. Become ruthlessly efficient and find data-driven ways to eliminate idle time and optimize your labor spend. ​
But that's not always easy to do if you don't have access to good data from your WMS or LMS.
In this step-by-step playbook, we’re going to walk through how our customers are getting more efficient, optimizing their processes, and getting more from their labor spend.
​
Or check out this interactive product tour to see some of our productivity functionality in action.
How it works
Take inventory of the operational processes in your warehouses
Find a way to measure and track all of your processes
Benchmark how much time and money you're losing to indirect activities
Tighten up long running breaks, lunches, and gap times around shift change
Address any indirect processes that are key causes of avoidable idle time
‍
The Playbook
Step 1: Map out all of your operational processes
Before you can improve anything you have to understand every activity that happens in your warehouse(s).
From core productive activities like picks, put aways, and replenishments, to indirect or support focused activities like battery changes, cleaning up spills, waiting on paperwork, or unloading mixed freight.
The good news is that you don’t have to fix everything at once! We always recommend taking a crawl > walk > run approach.
This usually looks like focusing on low hanging fruit like long running breaks and lunches or gap times around shift changes (more on that later).
‍
Step 2: Find a way to track all of these processes
If you use OneTrack, this part is easy. Talk to your implementation manager about configuring your activity codes to reflect different processes that you’d like to track.
By default these are set to track work, break, and lunch — but can be configured to almost any indirect process. Â
Operators simply sign into their equipment via a badge scan and then select a work code based on what process they’re completing.
If you don't use OneTrack to monitor and report on your processes in one place, your WMS and LMS are a good place to start for some of this information, but tracking indirect activities and idle time can be a challenge.
Pro tip: You can easily connect your WMS to OneTrack for further insights into your productivity, processes, and throughput.
‍
Step 3: See how much productive time you're losing to indirect activities
Now that you’re tracking your activities, let’s get a benchmark of the productive time and money we're losing.
OneTrack can show you this for a specific site or across your entire network. Let’s start at a network level.
Hop into the OneTrack dashboard > Reports > Click to Load a Report > LSW > Network Overview.
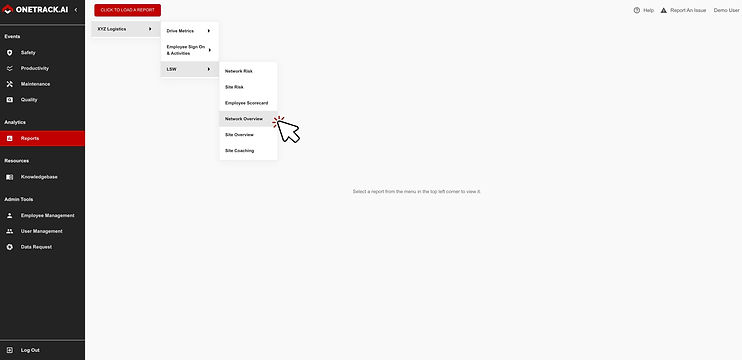
Do a quick filter by “Total Lost Time” — this will add up any gap, excess, or idle time throughout your warehouse network.
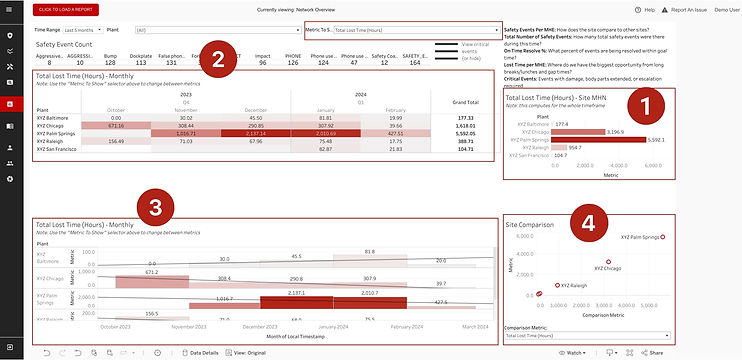
Now you can see a picture of your lost time, across your network:
- For the full time range
- Broken down by quarter
- Broken down my month
- A site comparison graph to see where your focus should be
​
This dashboard view will help you benchmark your network, track progress, and identify specific sites to focus your resources on.
‍
Step 4: Tighten up long running breaks and lunches
OneTrack has found that most warehouses lose hundreds — if not thousands — of hours of productive time, simply to operators taking extra time on their breaks and lunches from what’s allowed.
Let’s see just how much I'm losing.
Jump over to Reports > Employee Sign On & Activities > Opportunity Time. Filter by breaks and lunches.
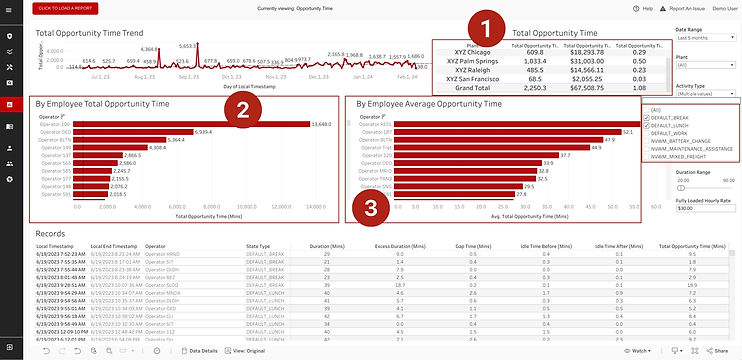
I can easily see across my 5 sites:
- I lost over $67,000 in the past 5 months that I had no clue about
- Total amount lost by operator to excessive breaks and lunches
- Avg amount of time lost by operator for excessive breaks and lunches
With that information I can have my site teams have specific coaching conversations with these operators and do some group training around company policies.
OneTrack also has SelfCoach that we can turn on to provide automatic coaching feedback when it identifies an exception — in this case a long running break or lunch. It has lead to some impressive results:
.jpeg)
‍
Step 5: Address other indirect processes that are causing avoidable idle time
Using that same report, I can also look at any other processes that I’m tracking.
Things like battery changes, waiting on paperwork, and unloading mixed freight.
One customer actually saved over $300,000 per year just by getting more visibility into their battery change process and changing when and how they occur.
For a more granular view hop over to Reports > Employee Sign On & Activities > Employee Activity.
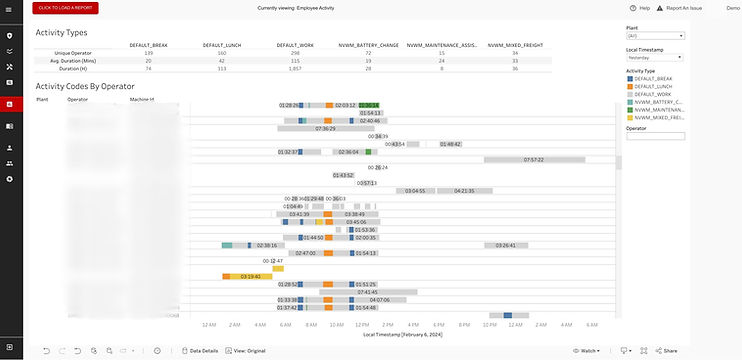
This lets you see every operator in a warehouse and what activity codes they were in throughout the day.
Now you can see process impediments and overlaps throughout the day. For example how long it actually takes to unload mixed freight and when those trucks typically come in. Or the fact that we could shift battery changes to occur during operators’ lunch to help save time.
This approach truly puts you in the driver's seat of your operations. Allowing you to understand processes, bottlenecks, and make key adjustments to keep things moving smoothly.
Not only do you create a more efficient workplace, you can virtually eliminate unnecessary idle time from process impediments and get the most out of your labor spend.
Want to put this playbook to work for yourself?
This playbook gives you the visibility you need to deeply understand your operational processes and get the most out of your labor spend.
In just a few minutes you now have data on:​
- How much time it takes across all of your key processes
- The amount of time and money you’re losing to total indirect time
- How much time you’re losing to long running breaks, lunches, and gap times
- What indirect processes are leading causes of idle time
That’s what Warehouse Intelligence is all about.
​
Want to put this kind of data to work in your warehouses?
OneTrack customers, good news! You already have this at your fingertips. Reach out to your implementation manager or support team with any questions.
If you aren’t a OneTrack customer, book a custom demo here. We’ll connect to better understand your operations and show you what a partnership could look like.
‍
‍