Take the Blindfold Off Your Warehouse Operation
GForce has been the “gold standard” in forklift telematics for a long time.
But are GForce forklift systems really the best option for reporting safety events to ensure your teams are kept safe and MHE in top condition? Not anymore.
The truth is, the rise of AI forklift safety systems (like OneTrack), have outpaced traditional forklift telemetry systems, and now offers way more to logistics leaders than GForce based systems ever did.
Let’s break it down.
What a GForce forklift system does
As the name suggests, GForce is the star of the show. The scientific version (according to Wikipedia) is “One ‘g’ is the force per unit mass due to gravity at the Earth's surface”.
I prefer the “Top Gun” version.
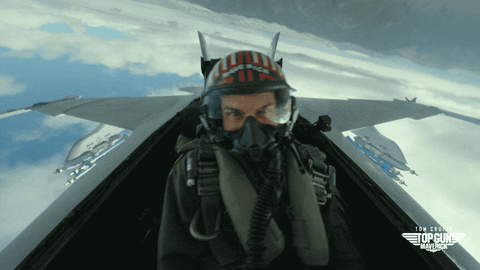
Essentially a measure of how we feel acceleration. The faster Maverick goes, the more “G's he’s pulling” which you can see on screen.
Forklifts aren’t exactly fighter jets, but the same idea holds.
GForce forklift systems use onboard GForce sensors to monitor acceleration (or sudden deceleration). The idea behind it is that if a certain GForce threshold is met, then an MHE incident probably happened, usually a forklift impact.
Most GForce forklift systems then lock out the MHE involved so it can’t be operated until a supervisor can unlock the lift.
These systems typically offer GPS forklift telematics as well to assist with things like fleet utilization and tracking.
What an AI forklift safety system does
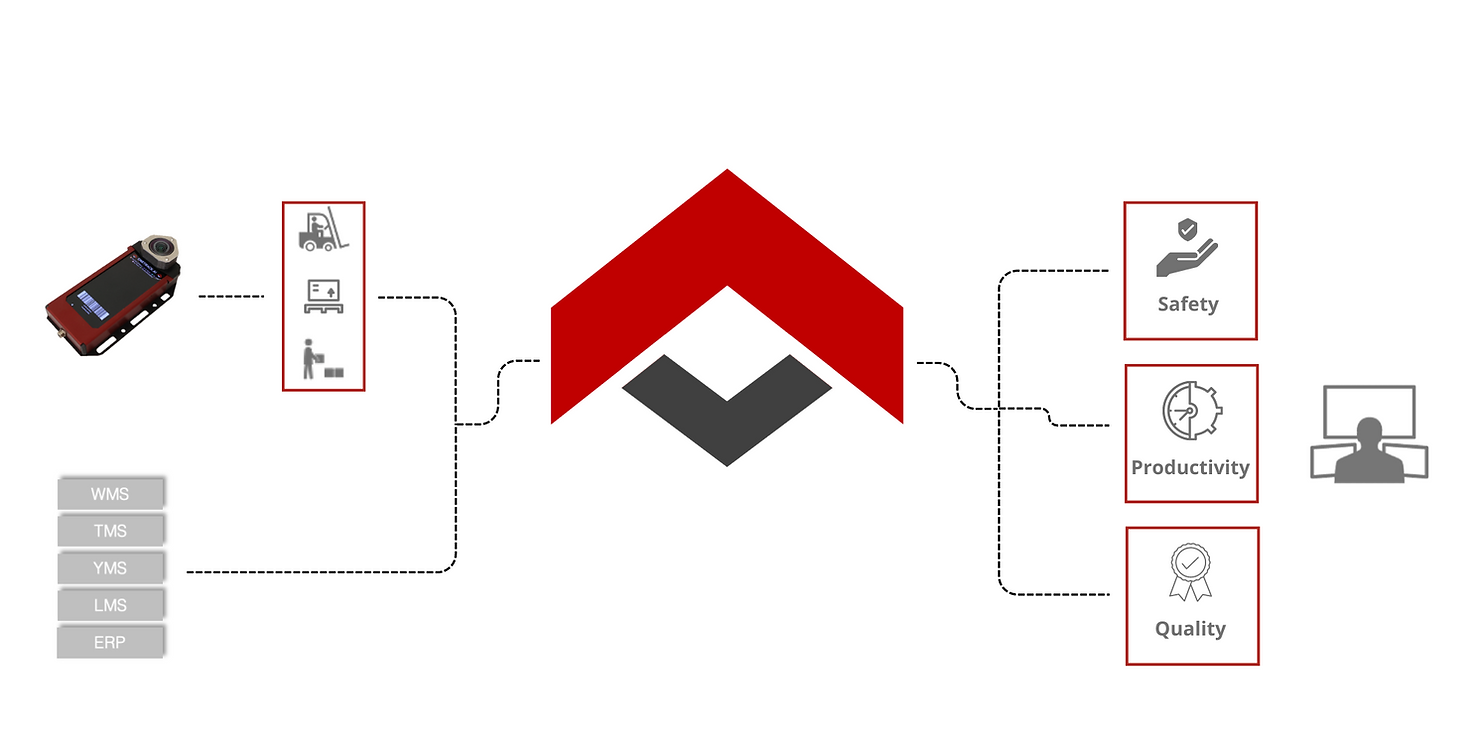
When it comes to forklift safety, OneTrack has taken a different approach from traditional GForce forklift systems.
OneTrack uses AI sensors that are mounted on your forklifts and other MHE. These sensors combine GForce, computer vision, GPS, and a number of other onboard sensors to collect real-time data about what’s really happening in your warehouse.
These sensors are monitored 24/7 by AI to detect when something goes wrong (like a forklift impact, an operator on their phone, or product damage), and then automatically sends an email alert to site leadership with a short video recording, so your team can view what happened and coach the operator in question.
Because we have trained our AI, OneTrack can even detect the leading indicators of MHE accidents, so you can proactively coach operators before a bad incident ever happens.
All of this is then fed into powerful reporting dashboards so you can identify trends and truly measure the culture of safety in your warehouses.
3 reasons why GForce forklift systems aren't enough today
We were using a telemetry system fleet wide for our forklifts and it was a disaster. And we knew it was a disaster because of the data that OneTrack started giving us. We ended up removing telematics from all our lifts and only using OneTrack for safety and fleet utilization.
- Mike Robson, Inland Star Distribution
1. GForce forklift systems only rely on... GForce
There’s a lot more to forklift impacts and safety incidents than just GForce.
Small bumps and scratches can severely damage product or increase wear and tear on MHE (and your maintenance budget) without ever triggering on GForce.
Not to mention missing the root causes and leading indicators of forklift safety. By just relying on GForce forklift systems you’re completely blind to operator phone use, distracted driving, or debris on the ground.
Coaching on these types of behaviors is what really moves the needle for warehouse safety.
2. GForce is a static number and can lead to false positives
In a perfect world it makes sense, right? You want to know when forklifts hit a GForce threshold, because that usually signifies an impact.
The problem is, warehouses aren’t perfect.
There are cracks in the ground (sometimes large ones), pallet debris or spilled product could be laying out, and dockplate maneuvers happen constantly.
Any of these common occurrences could set off a GForce trigger. Unfortunately these false positives lead to a few things:
- You have to turn down the GForce threshold so low that you miss a lot of actual impacts
- Employees start losing faith in GForce events and stop using the system
- False positives can lead to unnecessary lift shutdowns, which kill productivity and the bottom-line
You need a forklift safety system that’s built for the nuance of warehouse operations.
"It's one thing to have a system that just detects GForce or does a dash cam video. It's another thing to have it connected to a system that recognizes what's really an incident and what should my team spend their time on. And that's where OneTrack's AI really shines."
Brien Downie, Holman Logistics
3. There's only so much you can coach on with a GForce forklift event
A majority of GForce forklift systems don’t have any type of camera attached.
Because of that, when a GForce impact alert comes through, your team has no real way of knowing what actually happened.
Which means you can’t coach the operator or improve a broken process… which means it’s bound to happen again.
At best your team would have to cycle through hours of CCTV footage, hoping to catch a glimpse of what happened.
Even with the systems that have cameras, the angle is poor, no real-time notifications are sent out (so you can’t coach in a reasonable time), or like we mentioned before, employees lose faith in the system, and stop coaching altogether.
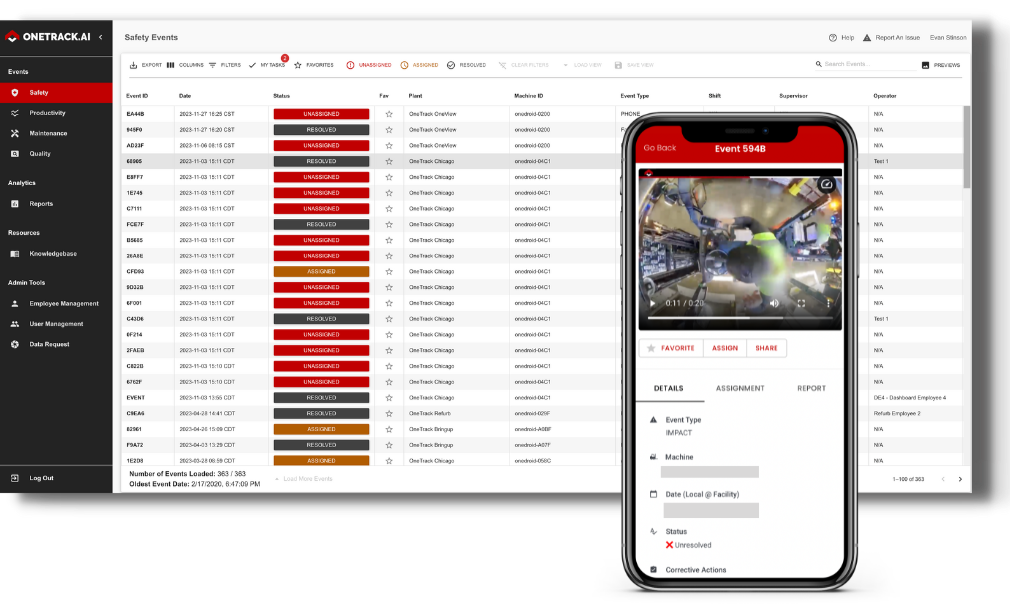
With OneTrack’s AI forklift safety solution you could get:
- 24/7 MHE monitoring with AI
- 360 degree video evidence of every safety event for actionable coaching
- Real-time alerts within minutes of an incident
- Alerts for leading indicators to proactively coach operators
- Customizable dashboards to track your safety programs and perform root cause analysis
Want to dive deeper? Check out how The Hain Celestial Group uses OneTrack to keep their warehouses safe and productive.
Or book a custom demo and we’ll show you how AI can upgrade your forklift safety.