Take the Blindfold Off Your Warehouse Operation
Walk through any warehouse in the world and I guarantee you’ll see scuffs on lift trucks and bent racking, but very rarely are you actually going to see it happening.
Every warehouse leader can agree that being able to detect and document more incidents is a good thing.
But what if you could identify the “almosts” — the leading indicators of safety incidents — and coach your operators before a serious incident ever happens?
That’s a game changer for warehouse safety, quality of service, and employee retention.
And it’s what we call having a critical eye.
The importance of proactive coaching to avoid MHE safety events
The typical process for employee coaching is reactionary.

An incident occurs > you find out about it > you talk to that employee about what went wrong.
This is still an important piece of the puzzle. Holding operators accountable and documenting incidents can do wonders for safety and quality.
However, it creates an inherently bad feedback loop. No one likes being punished, especially after a potentially traumatic safety incident. This leads to high turnover and limited effectiveness, especially when you don’t know what caused the incident. (Unless you catch it on a system like OneTrack.)
Instead, you need to take a proactive approach to operator coaching — cutting down on the bad habits that cause incidents, before they occur.
This truly makes supervisors coaches, rather than police, and allows for more open dialogue between supervisors and operators — they aren’t on the defensive trying to explain away an incident and will be much more open to feedback.
Don’t take our word for it. Watch how Holman Logistics uses OneTrack to keep their warehouses safe everyday.
Leading indicators of MHE safety events
After analyzing millions of safety events, we’ve found there are 4 main categories of leading indicators of MHE safety events.
Lack of personal protection equipment
Unsafe driving behavior
Distracted driving
Environmental factors
- Safety glasses
- Safety belt
- Hearing protection (if required)
- Safety harness (if required)
- High visibility vest
- Unsafe turning
- Aggressing stops
- Not looking in the direction of travel
- Both hands not on controls
- Clear dashboards around controls
- Headphones
- Scanner use
- Talking
- Typing into RF/computer
- Eating/drinking
- Vaping/smoking
Pallets, debris, or cracks on floor
No safety halo around lift
Not looking at intersections
Tight squeezes
Lack of personal protective equipment (PPE) - PPE policies exist to keep employees safe, but all too often, employees will forget to wear the required safety glasses, seatbelts, or high visibility vests, leading to more frequent — and worse — safety events. If an operator isn’t using the proper safety equipment, the video provided by OneTrack gives you the ability to see that and coach forklift operators in detail. This visibility is key to ensuring your forklift operators make it home safe every night.
Unsafe driving behavior - In general, forklift operators try to be as safe as possible while performing their daily tasks. Yet mistakes happen. These poor driving behaviors like speeding, harsh braking, aggressive turns, and not looking in the direction of travel happen everyday. Luckily, all can be flagged and reviewed within OneTrack.
Distracted driving - Just like driving a car, it can be easy to get comfortable in your routine. When you’re comfortable, you get distracted, and accidents can happen in the blink of an eye. The most common examples of distracted driving are phone use, headsets, or trying to use other equipment while driving.
Environmental factors - Warehouse environments are constantly changing. Factors like increased inventory, broken pallet pieces, debris, or even a crack in the floor can greatly increase the odds of an accident.
By spotting and coaching on these leading indicators you’ll be able to proactively avoid incidents by reducing bad habits in your warehouse, identify when processes break down or aren’t being followed, and find trends to provide additional safety training as needed.
How to use AI to increase forklift safety
With the help of camera sensors and AI you can prevent incidents before they occur by gaining a critical eye in your warehouse.
With a warehouse intelligence platform like OneTrack, you can get notifications whenever a safety event occurs, whether it’s an impact, bump, or dangerous driving.
These notifications present a unique opportunity. Think of them as a window into what’s really going on in your warehouse.
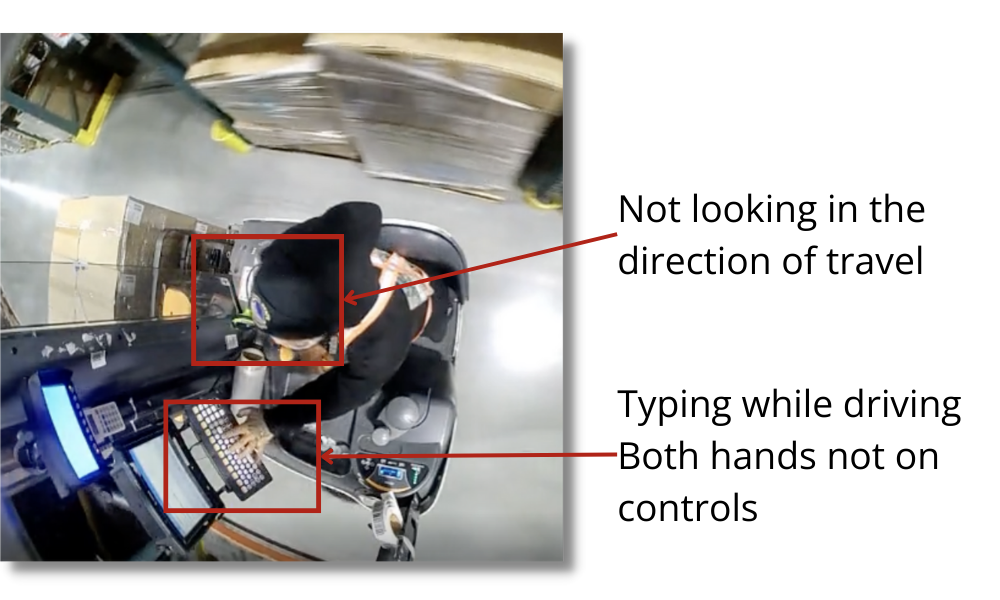
The system may flag someone for phone use while driving a lift, or for an impact — but you get a chance to dig deeper.
Was the operator wearing all of their PPE? Did they look while they were backing up? Were both hands on the controls, or were they also typing or using a scanner while driving?
These are real coaching opportunities for you to work with lift operators to instill the right habits and build a culture of safety and productivity in your warehouse.
Knowing when an incident happens is valuable, but the real power comes from knowing WHY.
With that critical eye, not only will the AI get better and better at flagging these leading indicators that are important to your operations, but you’ll get better at coaching forklift operators to ensure that everyone returns home safe and operations run smoothly.
Want to see how you can upgrade your warehouse and forklift safety with AI? Learn more here.