Take the Blindfold Off Your Warehouse Operation
Warehouse supervisors are the backbone of warehouse safety and productivity. But many lack the consistency and accountability needed to make a real difference at the site level.
Avoiding tough conversations and letting issues slide or making excuses puts everyone at risk.
Luckily, our customers have a few tips on how they up-level their supervisors and change the culture in their warehouses.
Here’s a look at three ways logistics leaders are using OneTrack to develop supervisors into true safety leaders.
Tip #1: Use video evidence and data to get hyper specific
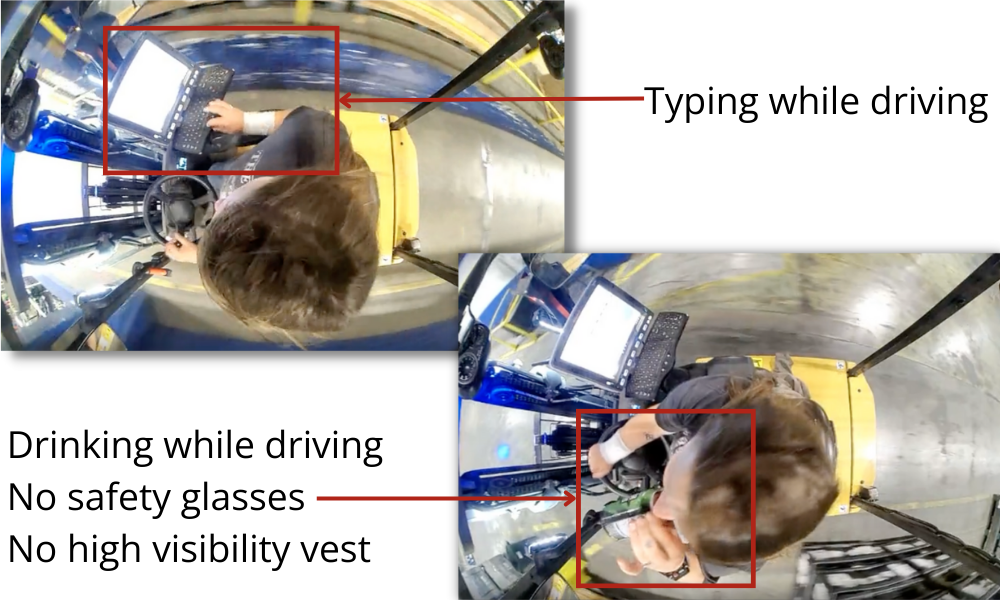
It’s one thing to give generic best practices in a safety meeting. But seeing video footage and real data for a specific site is a different matter.
Instead of broad hypotheticals, supervisors get hands-on coaching tailored to the exact situations their teams face daily.
Melody Moore, Director of Quality and EHS at Rinchem explained:
“We share short blurred video clips during company-wide safety meetings so everyone can learn from mistakes happening across different sites and we can improve our processes.”
Couple that with trend data to be able to see exactly how a site is trending with specific events, and you can start building safety programs around real challenges, and then holding supervisors accountable for delivering improvements.
Tip #2: Treat safety events like gamefilm
Video changes the dynamic of a coaching conversation. It’s not hypothetical, there’s no gray area or making excuses.
Matt Ireland, Director of EHS at Holman Logistics said, “Supervisors want to stick up for their team. But sometimes that means making excuses for them instead of coaching them. With video evidence, supervisors can’t make excuses for their team members. It helps them grow and be better leaders by holding people accountable.”
There’s a learning curve here though. You can’t just turn on video alerts and expect supervisors to be coaching experts out of the gate.
The whole team needs to learn how to take an incident and turn that into a constructive coaching opportunity. Sometimes operators don’t realize what they're doing is wrong.
It’s like a sports team. Coaches review gamefilm with the team after every game. That way you can talk through what went well, what went wrong, and what needs to improve.
It takes the emotion out of it and you’ll only get better the more you do it.
Tip #3: Hold supervisors accountable for their speed (and quality)
Coaching right after an event happens is way more effective than talking about it days after the fact.
But it’s easy for life to get in the way and put off a tough conversation for days (or never get to it at all).
Our best customers have implemented KPIs around speed to resolution and also quality of responses to hold supervisors accountable.
Expectations are set so when an event is detected by OneTrack’s AI software, it is expected to be resolved by the end of shift. This is also reviewed by the operations manager or warehouse manager in a dashboard every week to make sure that coaching is happening quickly and in the right way.
The Bottom Line
Safer warehouses start with better supervisors. But it’s your job to set your supervisors up for success.
Set expectations, lean into the data, and hold supervisors accountable to have those tough conversations using video evidence.
You’ll be shocked at how quickly your warehouse safety starts to improve.
Want to see how Hain Celestial reduced safety incidents by 80% with OneTrack? Learn more here.