Take the Blindfold Off Your Warehouse Operation
Keeping track of major accidents is important, but if you want to keep your warehouse teams safe, there are other safety events you need to keep an eye on and coach on.
Here are the 6 most common warehouse safety events we’ve seen across hundreds of warehouses in North America.
Or check out OneTrack's ultimate guide to building a video-based (and data-driven!) forklift safety program
Warehouse safety event #1: Phone use and distracted driving
Distracted driving is far and away the most common leading indicator of more serious accidents in a warehouse. Not to mention it can also be a productivity killer.
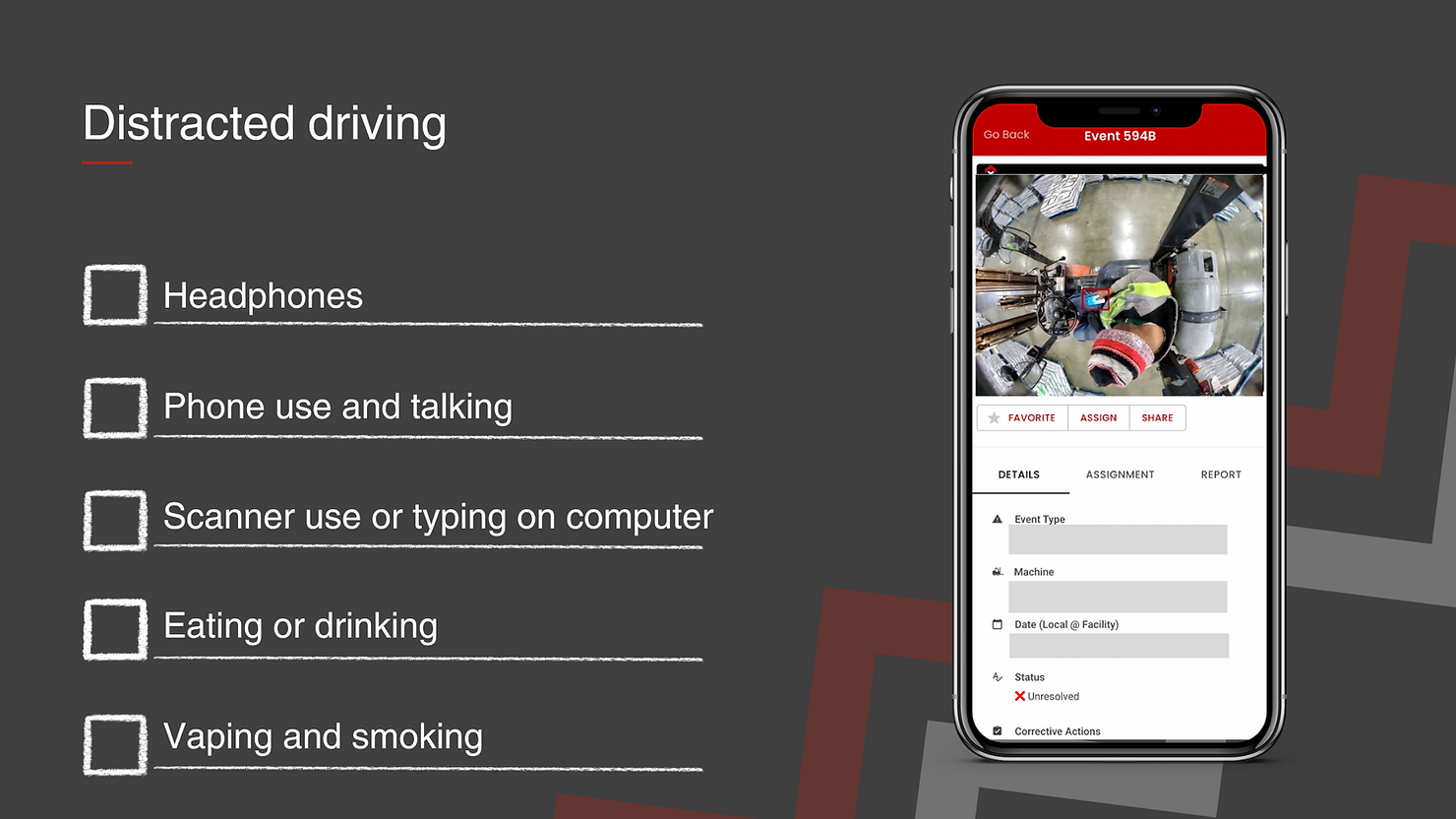
Phone use is the main culprit here, but things like eating, drinking, vaping, talking to other operators, or even just not looking in the direction of travel are all forklift safety events that your team needs a way to identify and coach on.
(Hint: A no tolerance phone policy alone isn’t going to cut it.)
Warehouse safety event #2: Hard forklift impacts
Hard impacts come in at #2 because they’re the most serious on this list.
We classify these as hard impacts with another forklift, hitting a pedestrian, or serious impacts with racking or columns. Long story short, these events are costly and dangerous.
Unfortunately, most warehouse leaders come into work and find damages (or even worse, a serious injury or workers comp claim) with no clue what really happened.
They investigate but employee stories don’t line up and they have to cycle through hours of CCTV footage trying to catch a glimpse of what happened.
See how Hain Celestial uses OneTrack to proactively monitor their warehouses and keep people safe.
Warehouse safety event #3: Soft forklift impacts
Soft impacts are an interesting thing to pay attention to. These are incidents like bumps against racking or scraping columns.
They wouldn’t trigger a traditional forklift telemetry system because the GForce wouldn’t register as high enough.
While these safety events don’t make the headlines, they're still important to identify and coach on for two main reasons.
- The soft forklift impacts of today could easily become the hard forklift impacts of tomorrow.
- This kind of wear and tear adds up on MHE equipment and can cost a fortune above and beyond your planned maintenance budget.
Warehouse safety event #4: Product hits
The next most common type of safety event that occurs in warehouses also doubles as a quality event: product hits.
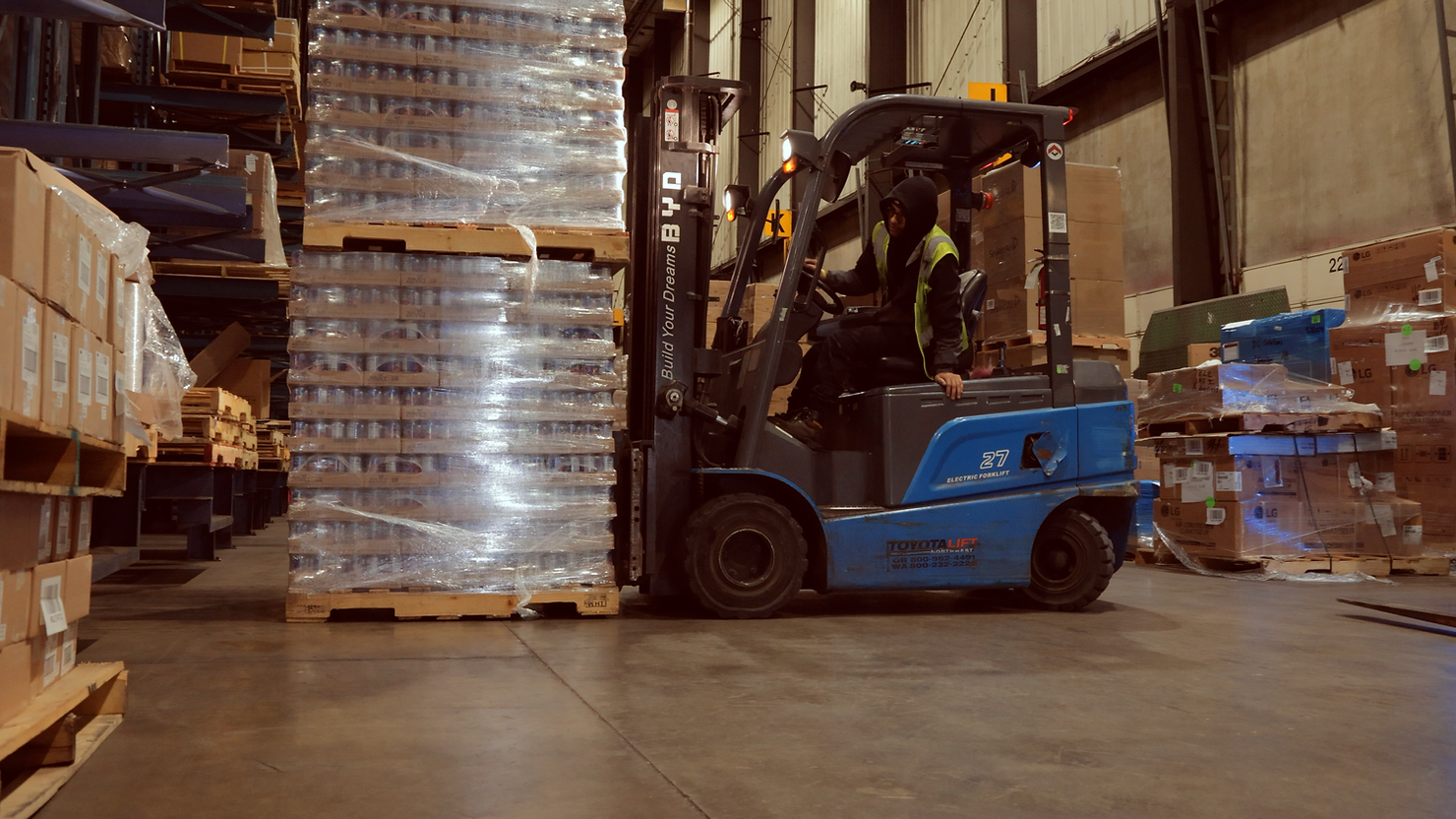
These are essentially hard and soft impacts, but rather than with other MHE equipment or racking, it happens with product. Typically it’s caused by tight corridors, a problem with how product is stored, or, most commonly, operators getting careless with forks during their moves.
This is an important event to track for several reasons. It’s obviously a problem when it comes to product quality and cost, but can also be a severe safety event when product falls on top of a lift or in the path of travel.
Warehouse safety event #5: Unsafe dockplate maneuvers
It happens everyday. An operator will go over a dockplate sideways, come out of a trailer forks out, or hit a dockplate at an unsafe speed.
This can cause the MHE to become unbalanced and tip over. Unfortunately these activities are incredibly hard to monitor unless you see it firsthand... or until it’s too late.
Plus with traditional forklift telematics we’ve found that customers often had to decrease the GForce sensitivity so much to avoid lift shutdown over cracks and dockplates that they miss the serious impacts.
But with a system like OneTrack, it can actually differentiate between a dockplate, a crack in the floor, or even broken pallets to only alert you when unsafe behavior is happening.
Warehouse safety event #6: Unsafe driving
We’ve all heard the stories of off shifts playing bumper cars with their forklifts — and while that’s not common (thankfully) — other unsafe driving behaviors are.
Excessive speeds, aggressive turning, harsh braking. These all seem like small problems (and they’re hard to identify and coach on consistently). But these unsafe driving behaviors put everyone in the area at risk.
Aggressive turns typically mean they didn’t check their surroundings fully. What if there’s a pedestrian approaching or a column that they didn’t spot?
With harsh braking, another lift could be coming up behind them and not expecting the sudden stop, or it can even dislodge product from the forks.
Long story short these unsafe driving behaviors need to be coached on early and often to ensure the safest possible warehouses.
Want more visibility into your warehouse operations?
These are the 6 most common safety events that we’ve found after working with hundreds of warehouses across North America.
Not all of them will show up on your OSHA reporting, but all of them deserve your team's attention — because the ultimate goal is to make sure everyone clocks out safely after every shift.
The problem is that tracking all of these safety events is incredibly difficult to do. Even with a large supervisor team on a constant roam through the building — incidents will still get missed.
Instead, top logistics leaders are turning to AI and computer vision to give them the deep visibility into their operations that they need to truly move the needle in their warehouse safety.
Want to see what this looks like in practice? You can take an interactive product tour here to see OneTrack in action on your own time.