Take the Blindfold Off Your Warehouse Operation
Does your warehouse still run on manually engineered labor standards? You might be losing millions on missed opportunities for performance improvements and cost reduction.
In today's labor-constrained environment, it is imperative that your warehouse workforce move as fast and accurately as possible. As a Thirdparty Logistics Provider (3PL), your clients demand faster turnarounds, higher volumes, and reduced OS&D claims every day.
Traditional engineered labor standards are broken because they only capture a single snapshot in time and they do not take into account the continuous change in priorities and operating circumstances of a real-world warehouse. After all, if there is one constant in warehousing and logistics, it is change and a never-ending shortage of new and unexpected challenges every day.
Engineered labor standards make a critical error in assuming:
- a static environment
- a constant labor force
- theoretical forklift travel paths
- consistent product types and storage solutions
- shipments that arrive in as-expected condition
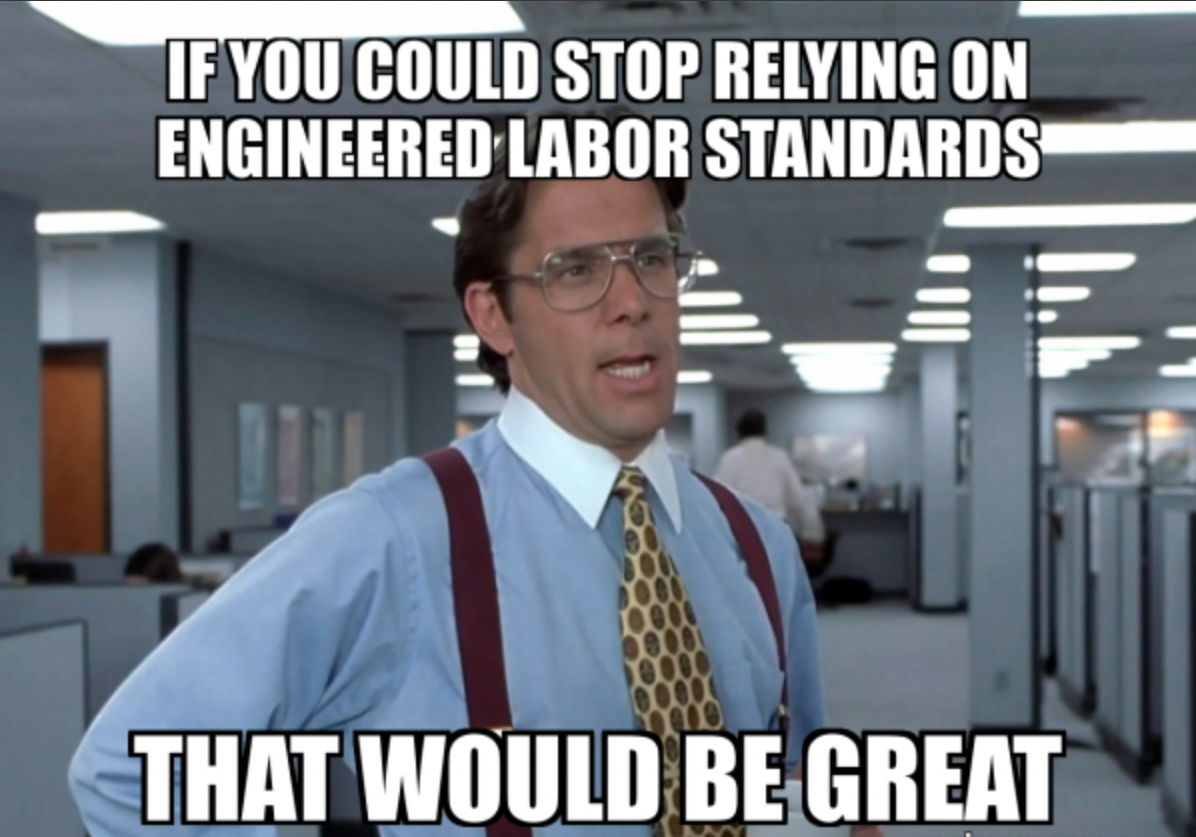
Even the most advanced engineered labor standards are fundamentally limited by the engineers who derive, measure and implement them. The formulas are usually out of date by the time they are implemented and humans simply cannot process and make sense of the thousands of real-time data points that are available in modern warehouses today.
As a result, most labor standards are inadequate, over-simplified, and inconsistent. The result has implications not just for productivity, but also for employee retention and development:
- How can you hold an employee accountable to performance goals that are not rooted in the current reality?
- How can management make HR decisions based on inaccurate performance data?
Ultimately, instead of coaching on the process, employees are coached on the outcome which creates a negative feedback cycle that results in higher turnover and lower employee retention. This comes at a high cost to 3PLs because every new employee needs to be trained, onboarded, and ramped up over and over.
Long story short, you simply won't make employees faster by telling them to work faster.
That is precisely where OneTrack's Artificial Intelligence Solution can unlock massive operational advantages for real-time labor management in high-throughput warehouses. Instead of relying on manually engineered formulas to determine baseline performance and expected productivity, a self-learning algorithm is used that processes millions of data points every day and learns what is normal and what is not, just as it occurs on the warehouse floor.
As a result, the system can pinpoint specific operational bottlenecks or coaching opportunities that fall behind the curtain of "aggregate data" in traditional labor standards. In addition, the more data is available, the more accurately the Artificial Intelligence Solution can identify outliers and underlying root causes, for example:
- Is it taking longer than expected to unload the inbound at door 24 because the airbags were not secured correctly and the load shifted?
- Is the case pick in aisle 17 running long because the operator ended up traveling down the aisle in the wrong direction?
- Is the cost per pallet skyrocketing on the third shift because the forklift operators take longer picking up pallets with their forks than usual?
- Is 60% of your travel distance spent navigating congested loading docks rather than traveling down aisles?
Over time, the Artificial Intelligence solution becomes better and more accurate at understanding the processes on your warehouse floor. Leveraging real-time data from systems like OneTrack's camera technology, it can adapt to the environment and external factors in real-time.
When combined with OneTrack's video-based AI performance management and remote coaching tools, productivity exceptions can be detected, recorded, and reported in real-time leading to instant improvement in productivity and labor cost per unit.