Take the Blindfold Off Your Warehouse Operation
So you want to increase productivity in your warehouses?
The formula is pretty simple.
Great people + rock solid processes + the right technology to support your strategy.
Unfortunately we all know that reality in the logistics world is anything but simple.
Processes break or become outdated, good talent is hard to find (and retain), and there’s a lot of technology out there that doesn’t live up to the hype.
But you can’t argue with data.
And after working with hundreds of warehouses, here’s 5 sure-fire ways our customers have increased productivity (all backed by data).
1. Don’t let shift changes kill your momentum
Even your most productive operators (on paper) can be guilty of it.
Idling at the beginning or end of their shift.
Whether they’re still trying to wake up and get in the swing of things or daydreaming about what they’re going to do after they get off work — it can add up to some serious productive time lost.
One of our customers found that they were losing over 2,400 hours every month across their network to gap times around shift changes and lunches. Now? They’ve been able to decrease that by more than 64% after just a few months of coaching.
2. Hold operators accountable for their breaks and lunches
An extra few minutes of a break or lunch here or there doesn’t seem like a big deal, right?
You have policies around these activities for a reason. And you’d be surprised at how much time you might be losing to long running breaks and lunches.
For example, one customer uncovered over $250,000 worth of productive hours lost to just long running breaks and lunches in 8 months.
Holding operators accountable to small processes like this can make a massive impact, but it all starts with more visibility and data.
3. Figure out which indirect activities you can optimize
Most of our customers find that their core activities (picks, putaways, replenishments, etc.) are actually pretty solid.
There’s anomalies of course that need adjustments and certain processes to improve, but overall they find it’s actually the indirect activities that cause the most opportunity time.
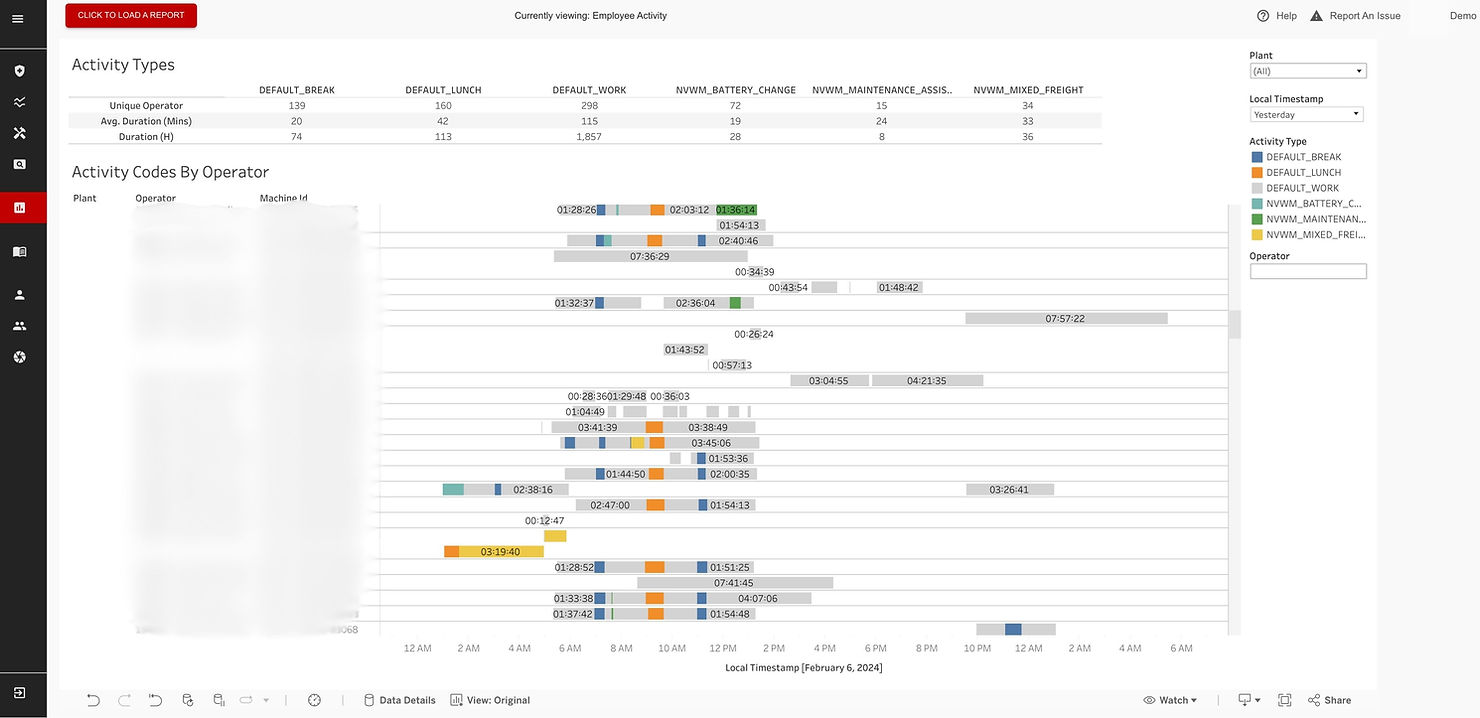
Using our activity tracking feature, one customer found they were losing more than $300,000 every year just to operators waiting on battery changes! And with a few process adjustments that number is almost $0 now.
Want a step-by-step playbook to eliminate idle time, skyrocket productivity, and optimize labor costs in your warehouses? Check it out here.
4. Ditch engineered labor standards for dynamic AI visibility
Engineered labor standards are broken.
They’re costly to set-up, require hours of manual time studies, and quickly become outdated when conditions change in your warehouse.
Which, quite frankly, happens about every 10 minutes.
What if you could use AI to learn and benchmark your specific operations to create dynamic labor standards that grow with you?
And got automated video alerts whenever a standard isn’t being met so you can actually see why a process took too long?
Plus in-depth heat maps and drive metrics to understand where breakdowns are occurring and how you can optimize your warehouse flow.
That’s the future of labor management. You can learn more here.
5. Give operators automated, real-time self-coaching
Speaking of engineered labor standards becoming outdated.
If there’s a problem in the warehouse — whether that be a process impediment, operators dragging their feet, or something else entirely — feedback needs to happen in the moment.
One way OneTrack is solving for this is through SelfCoach. Our sensors detect issues and deliver real-time, contextualized feedback.
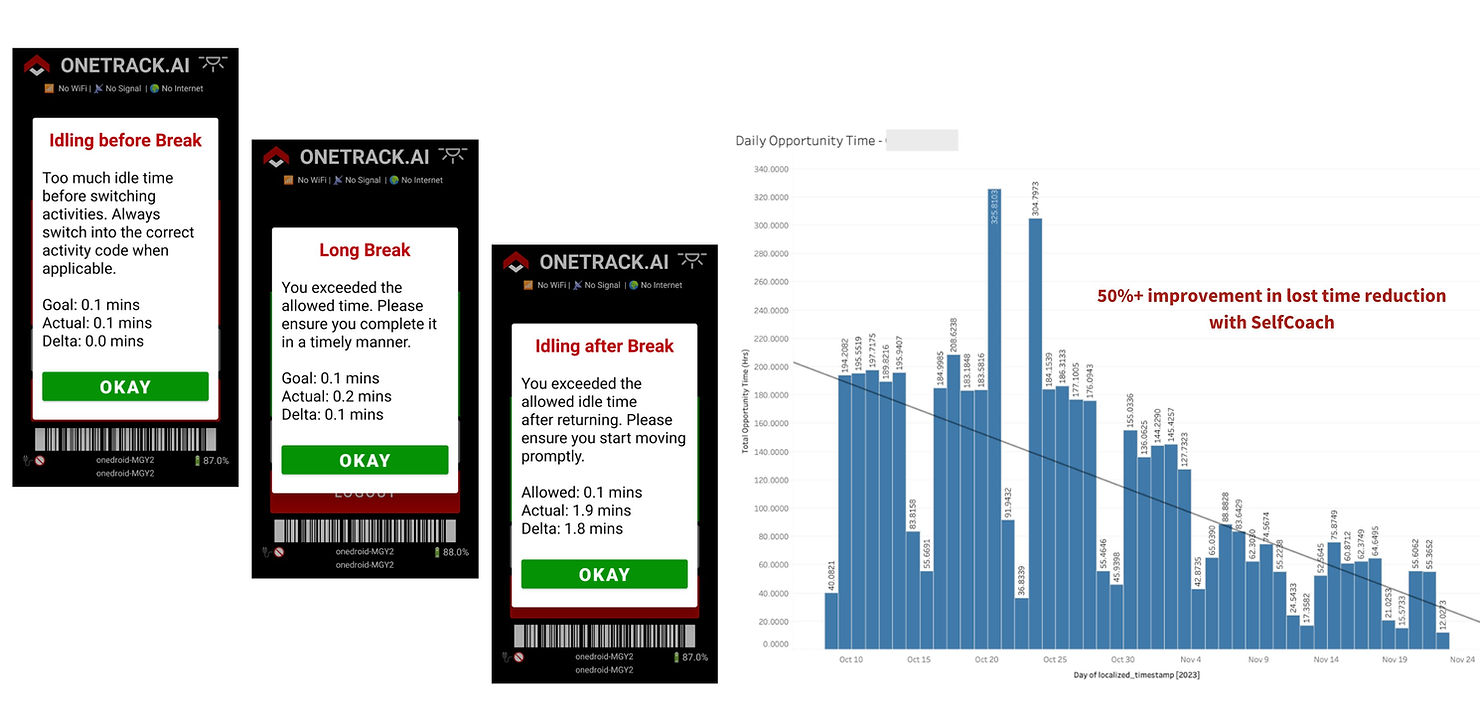
Could be as simple as an on screen notification letting an operator know that the 15 minutes extra they took on their break didn’t go unnoticed.
Or it could be an operator is stuck in a picking process because a spill happened and the sensor recognizes it and gives the operator the ability to escalate to supervisors for help.
Bottom-line
A productive warehouse is a profitable warehouse. But you need the right visibility and data so you can make better, faster decisions to improve operations.
Want a walkthrough of exactly how our customers are using data to improve their productivity?