Take the Blindfold Off Your Warehouse Operation
In July 2021, there were more than 490,000 open job postings for warehouse employees. Internal memos at Amazon show that executives are worried they might run out of available warehouse employees in certain regions.
In times like these, it is ever more important to focus on creating a culture of accountability and transparency. With the right tools and processes, every warehouse can focus on employee development to ensure every employee can become the best version of themselves.
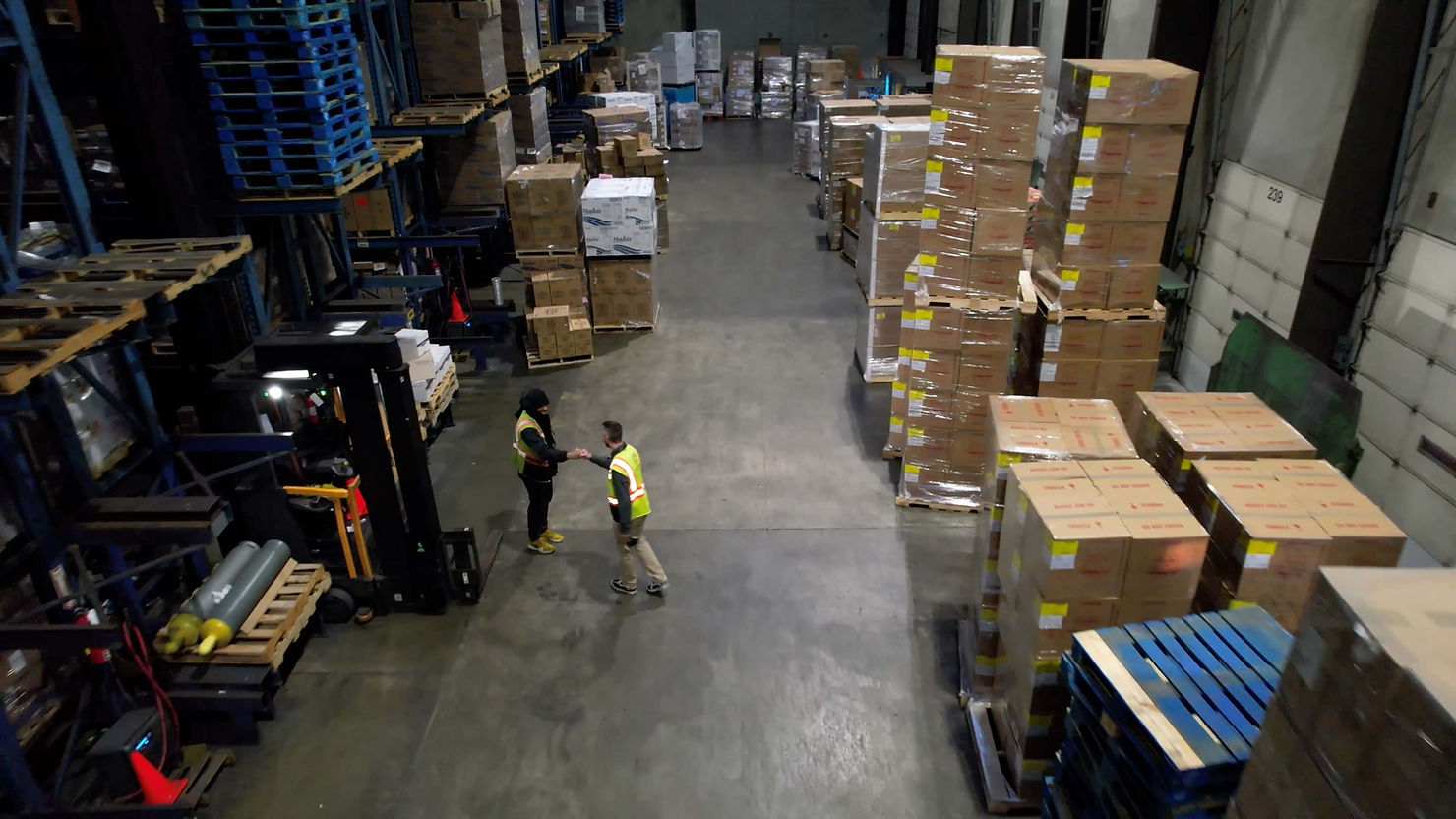
Here are 5 simple ways warehouse operators can focus on creating such a culture:
Training
Ensure that all employees receive adequate training on the equipment used in your warehouse. Comprehensive training can go a long way in ensuring operators feel comfortable in their jobs and that they understand how to use all systems, machines, and follow expected processes.
Safety Event Communication
Accidents are unavoidable, however, how you react to them is 100% in your control. Communicate clearly, review available video footage of safety events with all employees, and create site-specific training programs that address challenges, such as safety-event hotspots. This will help ensure that every new and existing employee understands how to be safe at work.
Manage with Data
Communicate goals and objectives widely and use dashboards and data to back up those plans and objectives. Presenting a comprehensive safety strategy that is more than just pencil-whipping form-filling, creates a culture of transparency. Presenting site-level performance data and highlighting root causes of bottlenecks or challenges helps foster a sense of community which reduces turnover.
Build progressive coaching workflows
Employees recognize when coaching is operator-specific and tailored to every individual's needs. Being able to reference an individual's specific challenges and opportunities during certain tasks can be key to further developing the relationships between supervisors and operators.
Promote self-reporting of issues and opportunities
Give every employee an opportunity to report safety issues, productivity bottlenecks, or process improvement opportunities. As a manager, and without 24/7 eyes on the warehouse floor, it can be difficult to understand exactly where the opportunities are in your building. Your employees are the most valuable source of information to identify and implement improvement opportunities - listen to them and let them help shape the workplace together.
OneTrack works with leading logistics companies to implement a data-driven safety culture and machine-learning-powered labor management. Using OneTrack's proprietary Artificial Intelligence technology, leading logistics companies are already fostering a culture of accountability, transparency, and continuous improvement which reduces their turnover and increases employee engagement.