Take the Blindfold Off Your Warehouse Operation
We often hear about initiatives at logistics and manufacturing companies to reduce travel distance in their material handling processes. Common areas of focus are:
- Inbound put-away
- Finished goods to outbound staging
- Case picking
When speaking with Process and Industrial Engineers, it is clear that the measure of forklift travel distance is very important because it is closely correlated with throughput. In an ideal world, reducing forklift travel should directly increase productivity since less distance has to be covered during every move.
The problem with travel distance is that there is little to no accurate data available. Engineers have to either rely on time-consuming, manual data collection using stopwatches, spreadsheets, and hand-drawn spaghetti diagrams or they have to simplify using theoretical travel distance based on the start and end locations of each task.
Neither of those approaches is particularly scalable or effective. By the time all data has been captured, the warehouse has probably already changed and many calculations are moot.
That is precisely where Computer Vision can help. Using Computer Vision technology, it is possible to establish real-time location data without any external infrastructure. A Computer Vision powered localization system can keep track of the position of a camera using only visual clues. No beacons, markers, or other systems are required.
Real-time location data captured by OneTrack Sensors completely changes the game when it comes to process optimization. Now, instead of relying on static, outdated data, engineers can design, optimize, and track processes using accurate travel path information.
Process optimization opportunities can be pinpointed to certain areas in the warehouse based on the actual travel paths of each and every forklift. This data can be visualized in the form of a heatmap and updated in real-time to provide accurate location data that shows how a building's travel paths are changing over time.
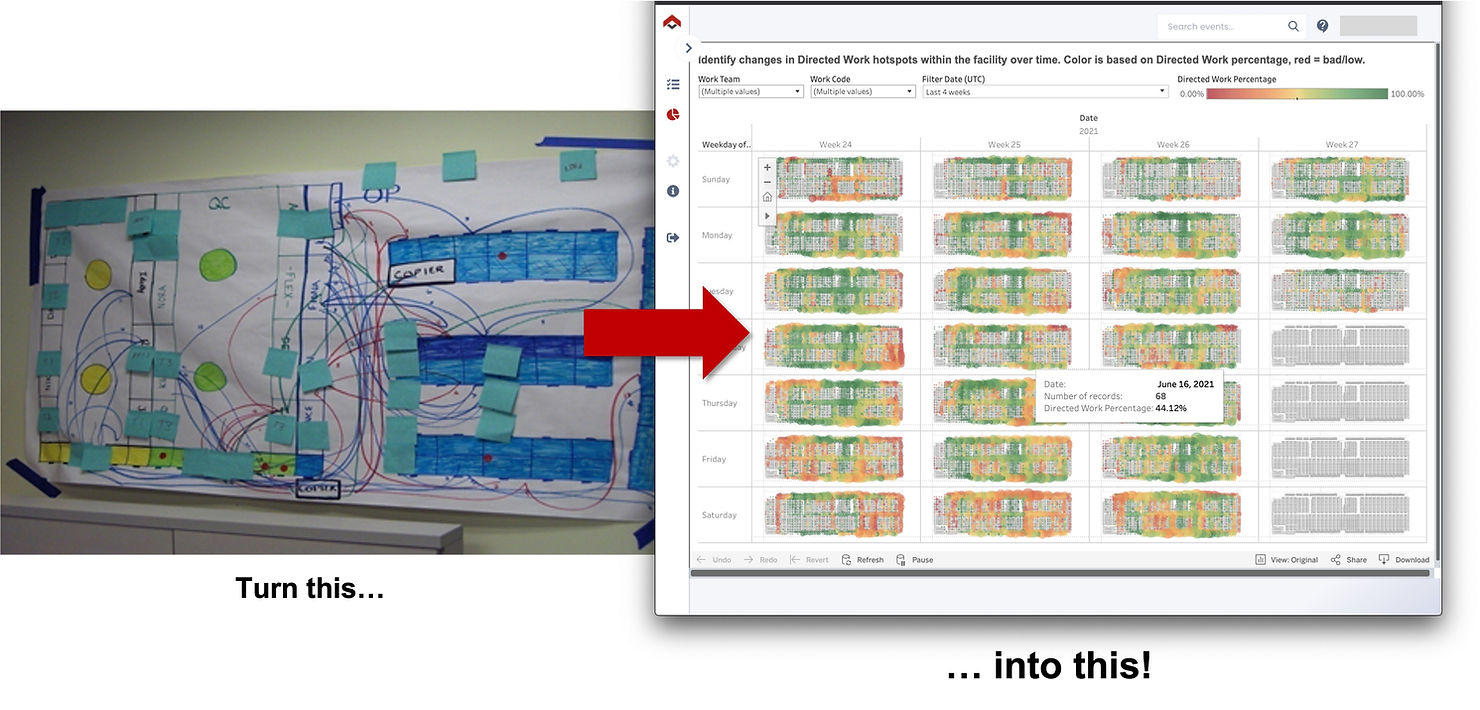
In addition to tracking where travel is occurring in the warehouse, the data can also be used to drive employee-coaching opportunities to help increase productivity.
Using OneTrack's Artificial Intelligence enabled Labor Management Solution, it is possible to identify travel path outliers and build workflows that focus on travel-specific coaching.
For example, employees who drive inefficiently across the building or take longer paths than necessary can be identified and tracked automatically. Using video data from OneTrack sensors, significant travel exceptions can be recorded, reviewed, and corrective actions can be taken to improve that particular employee's performance. By continuously focusing on an employee's travel, their overall efficiency can be increased, ultimately reducing labor cost per unit.
If you want to learn more about measuring and optimizing forklift travel in warehouses, book a demo!