Take the Blindfold Off Your Warehouse Operation
Dylan O'Connor
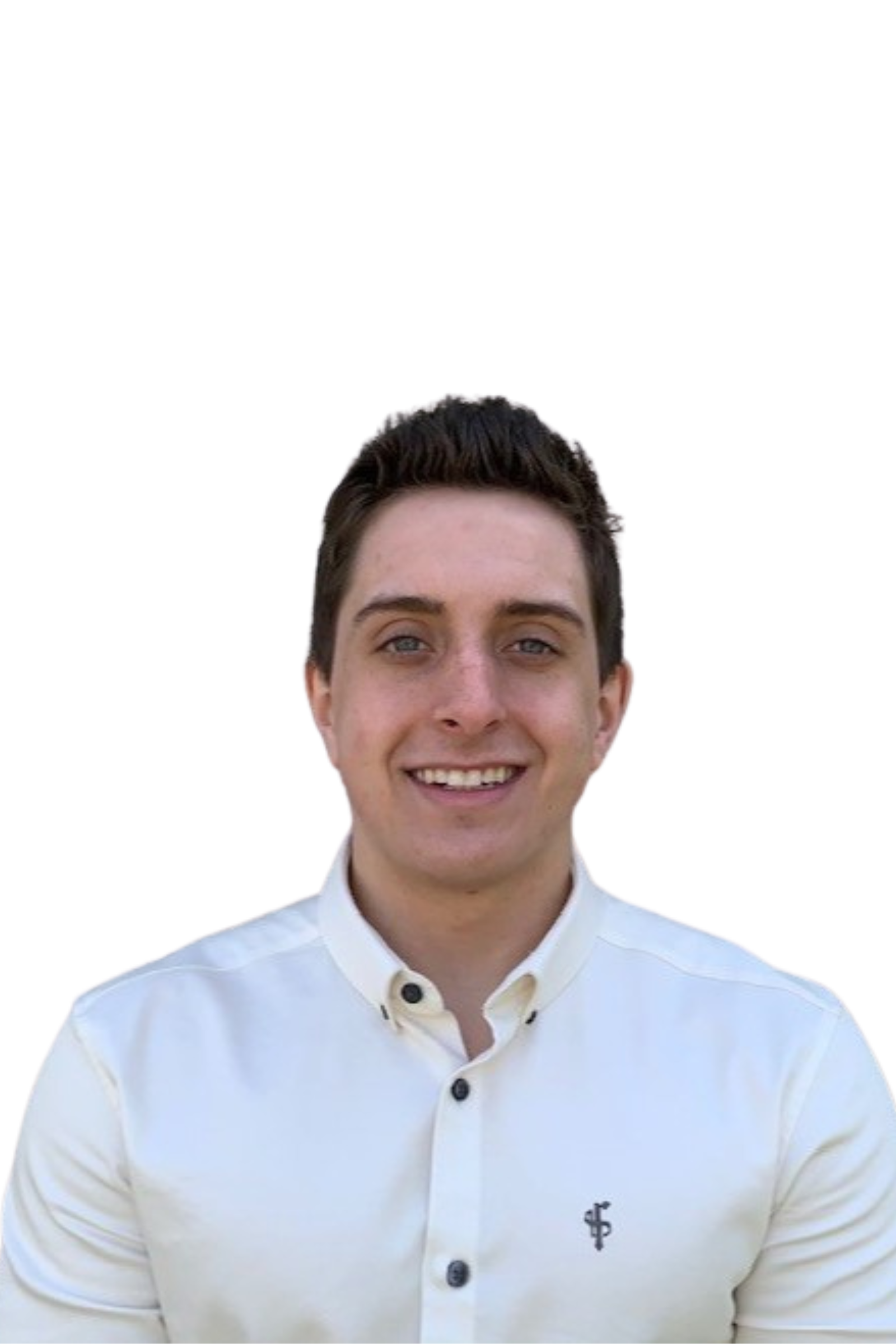
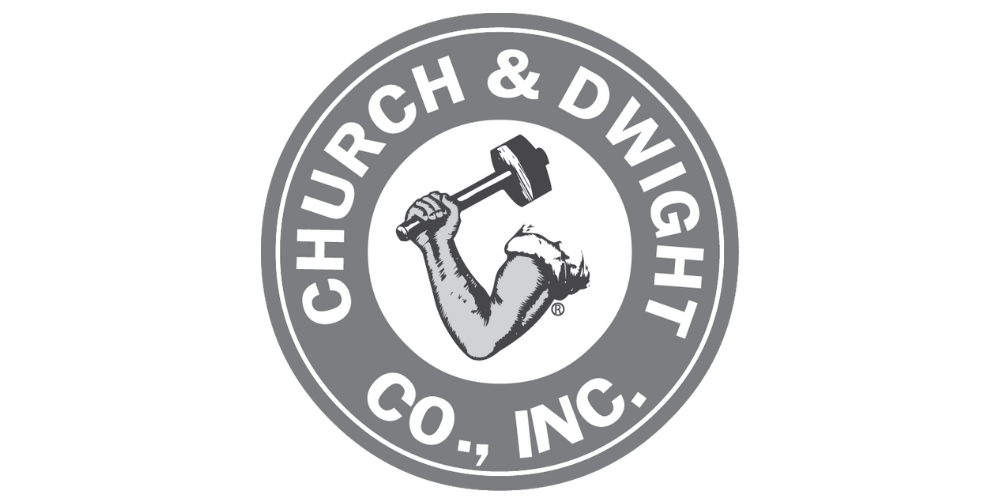
The Challenge
At over 1.1 million square feet, Church & Dwight’s York site is the company’s largest facility — shipping 50% of all domestic volume. But with 250 operators, 96 forklifts, and a nonstop pace, leaders struggled with visibility into everyday operations.
Manual tracking methods made it nearly impossible to catch exceptions in real time — especially when it came to break compliance, load quality, and coaching consistency.
“We knew there was some abuse with 15-minute breaks, but no hard data. You’d look at system gaps and think — how is the break the same length as lunch? That’s not right.”
— Dylan O’Connor
At the same time, supervisor bandwidth was stretched thin. Coaching moments were missed. Performance reviews lacked structure. And root causes were left unknown.
‍
The Solution
OneTrack AiOn: AI Agents Built for Operations
Church & Dwight deployed OneTrack with a focus on improving safety. But within weeks, AiOn — OneTrack’s AI Agent Platform — became the operational game-changer.
Today, AiOn automates daily workflows once done manually (or not at all):
- Break & lunch compliance is now fully tracked via video + movement data
- Supervisor alert are automatically sent for policy violations
- Weekly safety reports and new hire 60-day reviews are generated by AI
- Loading footage is recorded automatically to protect operators and pinpoint carrier-related damage
“The agents don’t just find issues — they give our supervisors the exact coaching points and even recognize wins. We were losing 120 hours a week just on extended breaks. Now, AiOn flags violations and sends them directly to supervisors. That alone pays for OneTrack.”
— Dylan O’Connor
‍
The Results
Measurable ROI in Under 5 Months.
Since rolling out AiOn, Church & Dwight has seen immediate results across compliance, productivity, and quality:
- Gap Time120+ weekly hours saved by automating break/lunch compliance
- Cost Savings$287,000 in annual cost savings from gap time savings
- Proactive CoachingShifted from reactive discipline to proactive coaching
- Load QualityVideo exoneration for operators on improperly blamed load issues
- Consistent ReviewsStandardized 60-day reviews now delivered via AI
- Spills and Product DamageSpill root-cause analysis done in minutes not hours
“We used to go off gut feel. Now we have data — and it’s automatic. The system even picked up a legitimate idle event where an operator was helping clean a spill. AiOn told us to thank him. That’s next level.”
— Dylan O’Connor
‍
Church & Dwight and OneTrack: A New Era of Operations
Effortless Operations.
AiOn handles the data work — summarizing exceptions, flagging patterns, and delivering insights to the floor.
Smarter Supervision.
From 60-day reviews to daily alerts, OneTrack ensures consistency and structure across shifts — freeing site leaders from detective work.
AI that Gets Better Every Day.
As Church & Dwight connects more systems — like WMS — AiOn will scale further: analyzing productivity, building optimization, and other trends that humans don’t have the time for.
“It would suck going back to the way things were. We’d be blind without OneTrack. We’re just getting started — and we’re already miles ahead.”
— Dylan O’Connor